Post-vulcanization, a thorough inspection is mandatory. Hoses are subjected to rigorous testing — pressure tests, fatigue tests, and bend radius tests ensure they conform to industry standards and specifications. Only products that pass these stringent evaluations proceed further. Testing certifies each hose's reliability and builds trust with clients who depend on the hose's performance in critical operations. The final stages include finishing touches such as printing — where vital information like size, pressure capacity, and batch number is inscribed for traceability. Some hoses even receive special coatings to enhance properties like UV resistance or to provide additional chemical protection. Quality assurance teams, skilled in the science of metallurgy and chemistry, oversee these final steps with an authoritative eye, ensuring the hose meets all regulatory compliances. Adopting sustainable practices is gaining momentum across the industry. Hose manufacturers now focus on reducing waste during production, utilizing renewable energy sources, and implementing recycling programs for offcuts and defective items. Such initiatives resonate with environmentally conscious consumers and businesses seeking sustainable partnerships, reinforcing the manufacturer’s commitment to preserving our planet's resources. In conclusion, the hose manufacturing process is a harmonious blend of traditional techniques and modern innovations. It demands expertise and accuracy at every stage, from material selection to final inspections. Manufacturers that master these processes deliver products that clients can trust, demonstrating unwavering commitment to quality, reliability, and sustainability. The authoritative execution of these procedures by seasoned professionals ensures that the hoses meet the highest standards, even under the most demanding conditions. As the world continues to evolve, so too will the hose manufacturing industry, innovating in ways that enhance safety, efficiency, and sustainability for generations to come.
Previous:
OUR LATEST NEWS
Strict quality control strict production team to ensure stable products quality. Scientific personnel management, efficient production arrangements to ensure our timely delivery.
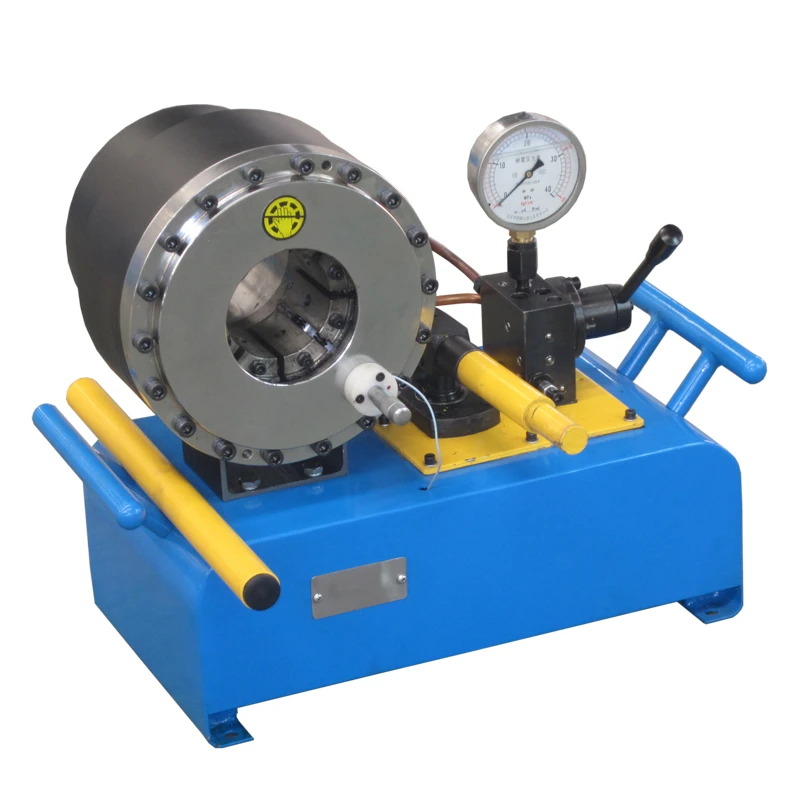
Apr 11 2025
A Comprehensive Guidance of Manual Hose Crimping Machine
A manual hose crimping machine is an essential tool in the hydraulic hose assembly process. It is designed to securely attach fittings to hydraulic hoses by applying controlled pressure, ensuring leak-proof and durable connections.
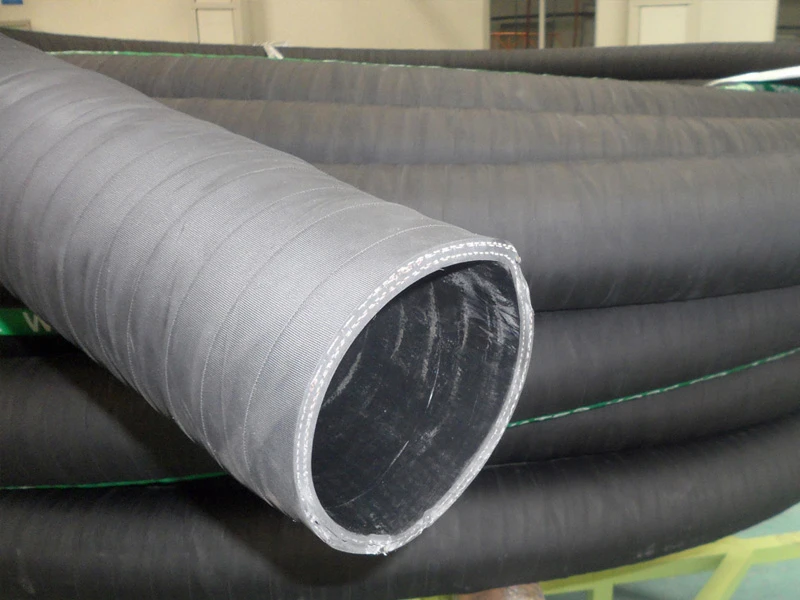
Apr 11 2025
Industrial Hose Types and Uses
Industrial hoses are critical components designed to transport liquids, gases, and abrasive materials across various industries, including construction, manufacturing, and oil and gas. The different types of industrial hoses are engineered to meet specific operational demands, such as pressure resistance, flexibility, and durability.
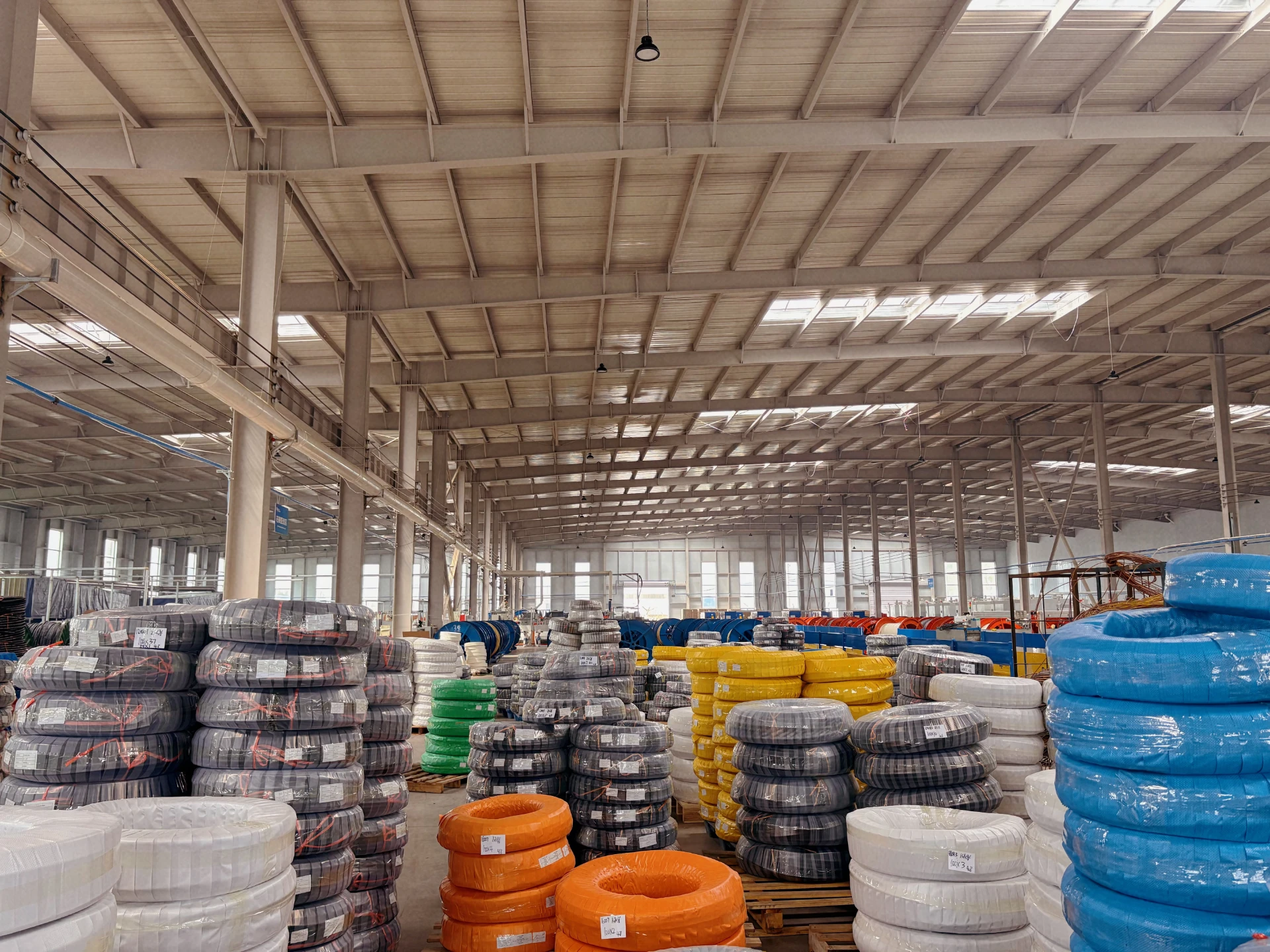
Apr 11 2025
The Essential Guide to Custom Hydraulic Hoses for Industrial Applications
Custom hydraulic hoses are essential components in hydraulic systems across various industries, designed to efficiently transport high-pressure hydraulic fluids between system elements. Unlike standard hoses, custom hoses are tailored to specific requirements, such as pressure, environmental conditions, and mechanical constraints.
Product Application