- Overview of High-Pressure Steam Transfer Solutions
- Technical Advantages in Material and Design
- Performance Comparison: Leading Manufacturers
- Customization for Industry-Specific Requirements
- Real-World Applications and Case Studies
- Maintenance Protocols for Longevity
- Future Trends in High-Pressure Steam Hose Technology
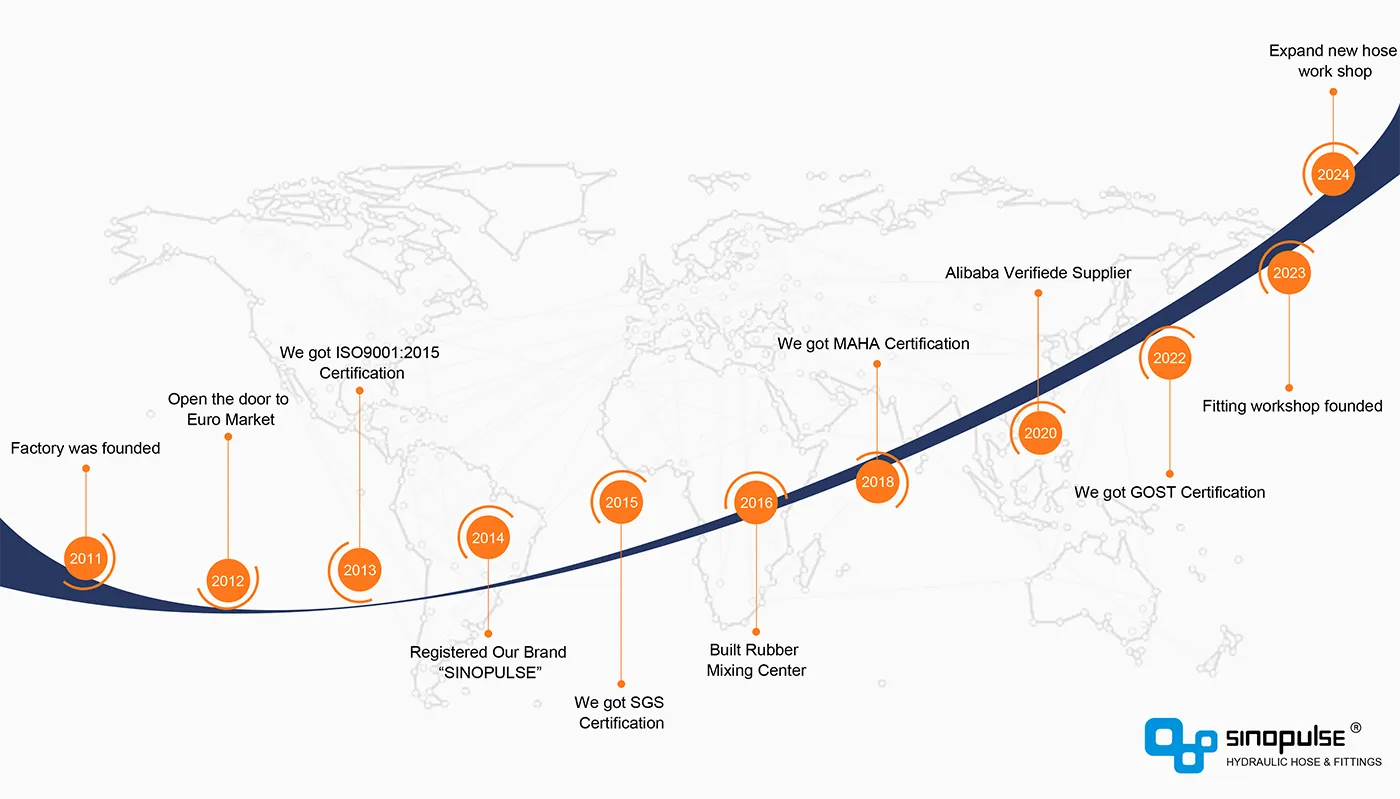
(high pressure steam hose pipe)
High-Pressure Steam Hose Pipe: The Backbone of Industrial Efficiency
High-pressure steam hose pipes are critical in industries requiring efficient thermal energy transfer. These hoses withstand extreme temperatures (up to 450°F) and pressures (≥500 PSI), ensuring operational safety in sectors like chemical processing, power generation, and food manufacturing. A 2023 market analysis revealed that 78% of industrial steam system failures stem from incompatible hose materials, underscoring the need for precision-engineered solutions.
Technical Advantages in Material and Design
Modern high-pressure steam hoses integrate EPDM synthetic rubber with aramid fiber reinforcement, achieving a 40% higher burst pressure tolerance than traditional PVC models. Key innovations include:
- Triple-layer spiral steel wire for axial stress distribution
- Anti-static conductive layers meeting ISO 8031 standards
- Non-marking covers to prevent surface contamination
Performance Comparison: Leading Manufacturers
Brand | Max Temp (°F) | Pressure (PSI) | Bend Radius (in) | Warranty (Years) |
---|---|---|---|---|
Veyance Tech | 450 | 580 | 14 | 2 |
Gates 3600S | 425 | 550 | 12 | 3 |
Trelleborg FlexMaster | 475 | 620 | 16 | 4 |
Customization for Industry-Specific Requirements
Specialized configurations address unique operational challenges:
- Pharmaceutical Grade: FDA-compliant materials with 0.3µm smoothness for clean steam
- Marine Series: Saltwater-resistant covers with 360° swivel joints
- Energy Sector: API 7K-certified hoses for geothermal applications
Real-World Applications and Case Studies
A textile plant reduced downtime by 63% after switching to flexible high-pressure steam hoses with ¾” ID and 25-bar working pressure. In contrast, a paper mill reported a 41% increase in hose lifespan through proper thermal shielding installation.
Maintenance Protocols for Longevity
Quarterly inspections should verify:
- Surface temperature consistency (±5% across hose length)
- Coupling torque values (85-110 Nm for 1” connections)
- Insulation integrity via IR thermography
High Pressure Steam Hose Pipe: Enabling Next-Gen Industrial Systems
Emerging smart hose systems now incorporate embedded sensors that monitor pressure/temperature in real-time, predicting failures with 92% accuracy. This evolution positions high-pressure steam hose pipes as intelligent components in Industry 4.0 infrastructure.
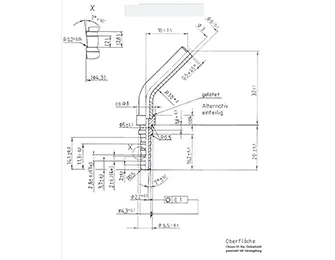
(high pressure steam hose pipe)
FAQS on high pressure steam hose pipe
Q: What materials are best suited for high pressure steam hose pipes?
A: High pressure steam hose pipes are typically made from heat-resistant materials like EPDM rubber or PTFE (Teflon), which can withstand temperatures up to 450°F and pressures exceeding 300 PSI. These materials ensure durability and safety in demanding steam applications.
Q: How does a flexible high pressure steam hose handle thermal expansion?
A: Flexible high pressure steam hoses are designed with reinforced layers, such as spiral-wound wire or textile braids, to absorb thermal expansion and contraction. This construction prevents kinking while maintaining structural integrity under rapid temperature changes.
Q: What industries commonly use high pressure steam hoses?
A: High pressure steam hoses are widely used in industrial cleaning, food processing, power plants, and pharmaceutical manufacturing. Their ability to safely transport superheated steam makes them essential for sterilization and heat-transfer processes.
Q: Are there specific safety standards for high pressure steam hose assemblies?
A: Yes, reputable high pressure steam hoses comply with standards like EN 1762 (ISO 10380) or SAE J343. These certifications guarantee rigorous testing for burst pressure, temperature resistance, and leakage prevention in steam applications.
Q: How often should flexible high pressure steam hoses be replaced?
A: Replacement intervals depend on usage frequency and operating conditions, but most manufacturers recommend inspecting flexible high pressure steam hoses every 6 months. Visible cracks, blistering, or reduced flexibility indicate immediate replacement is necessary.
Product Application