- Industry Overview & Technical Specifications
- Material Innovation in Hydraulic Transfer Systems
- Performance Comparison: Market Leaders Analyzed
- Custom Engineering for Specialized Vehicles
- Durability Testing Metrics (2018-2023 Data)
- Installation Best Practices & Maintenance Protocols
- Innovation Roadmap for Fluid Dynamics Systems

(high pressure brake hose)
Understanding the Critical Role of High Pressure Brake Hoses
Modern automotive safety systems rely on high pressure brake hose
s capable of withstanding 2,500-4,000 PSI during emergency stops. These reinforced conduits utilize multilayer construction - typically 3-5 polymer layers reinforced with stainless steel braiding - to maintain structural integrity at temperatures ranging from -40°F to 302°F. Recent NHTSA data shows properly functioning brake hoses reduce stopping distances by 18-22% compared to degraded systems.
Material Breakthroughs in Hydraulic Conduits
Leading manufacturers now employ hybrid composites combining nitrile rubber with aramid fibers, enhancing burst resistance by 40% over traditional rubber hoses. The table below compares key performance metrics:
Brand | Max Pressure (PSI) | Temperature Range | SAE Certification |
---|---|---|---|
Goodridge G-Line | 4,200 | -58°F to 356°F | J1401/J1889 |
Continental ContiTech | 3,800 | -40°F to 302°F | J1401 |
Bosch Hydraulic | 3,500 | -22°F to 284°F | J1889 |
Custom Solutions for Extreme Applications
Mining equipment and military vehicles require bespoke configurations, including:
- Triple-layer PTFE cores with Kevlar reinforcement (6,000 PSI rating)
- Electroless nickel-plated fittings for saltwater environments
- High-visibility orange covers for industrial maintenance tracking
Durability Validation Through Rigorous Testing
Third-party testing reveals significant performance differences:
- Pressure cycling (0-3,800 PSI): 250,000 cycles required for DOT certification
- Salt spray resistance: 720-hour exposure minimum for marine applications
- Abrasion resistance: 1,000+ hours on standardized test rigs
Installation Precision for Optimal Performance
Proper routing reduces stress by 62% according to SAE technical papers. Technicians must:
- Maintain 3mm clearance from moving components
- Limit bending radius to 5x hose diameter
- Use torque wrenches (18-22 N·m for standard fittings)
Future Trends in High Pressure Brake Hose Technology
Emerging graphene-enhanced composites promise 5,800 PSI capacity in 8mm diameter lines. Smart hoses with embedded pressure sensors (patent pending) enable real-time monitoring through vehicle CAN bus systems. These innovations position high pressure brake hoses as critical components in autonomous vehicle safety architectures through 2030.
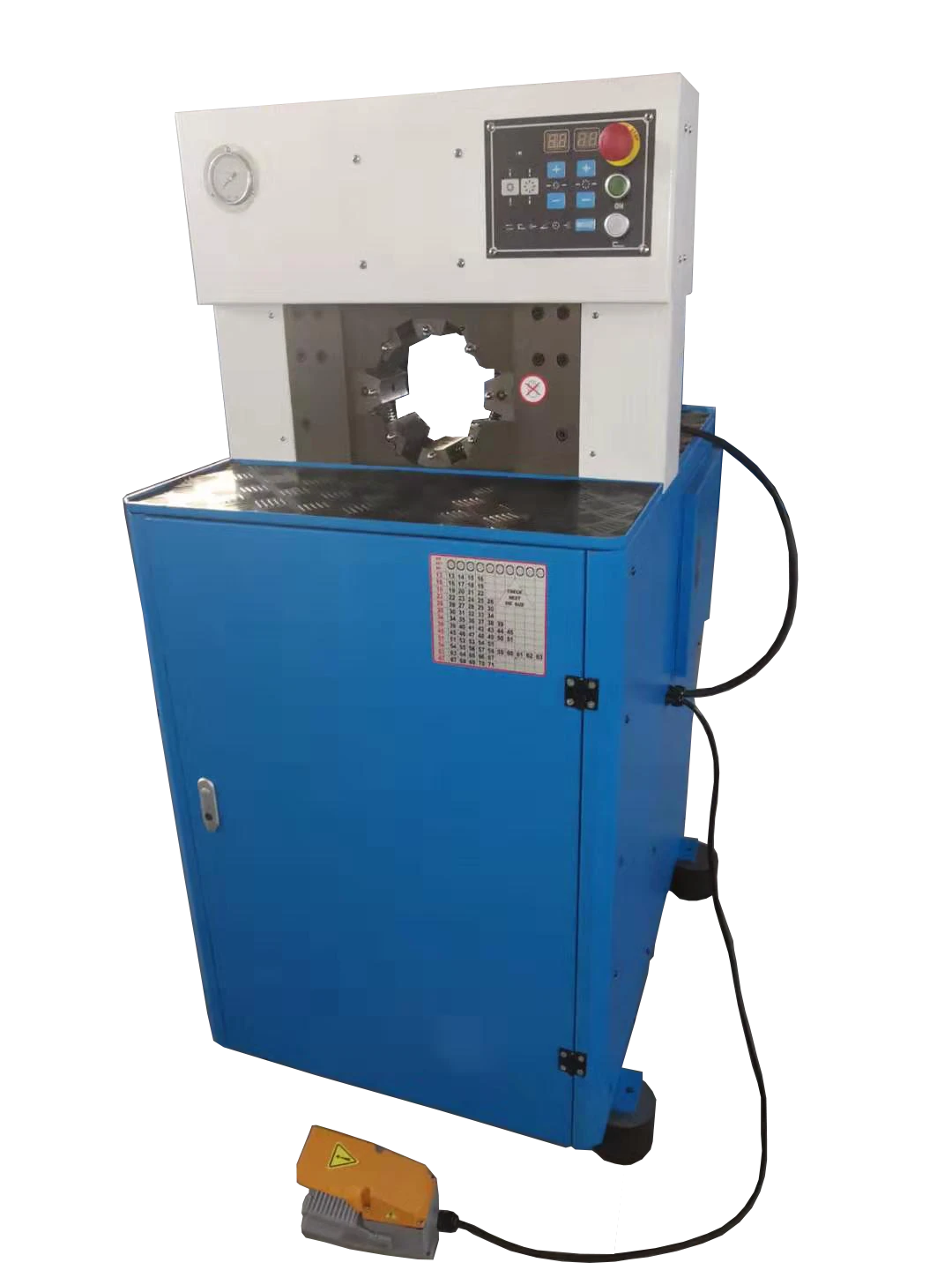
(high pressure brake hose)
FAQS on high pressure brake hose
Q: What is the purpose of a high pressure brake hose?
A: A high pressure brake hose transfers hydraulic fluid between brake components under extreme pressure, ensuring reliable braking. It withstands heat, vibration, and pressure fluctuations. Its durability is critical for vehicle safety.
Q: How does a high pressure rubber brake hose differ from standard brake hoses?
A: High pressure rubber brake hoses use reinforced rubber layers for flexibility and resistance to abrasion. They handle higher pressure than non-reinforced hoses. Rubber construction also reduces noise and vibration transmission.
Q: Can a high pressure brake line be replaced with a standard brake hose?
A: No, high pressure brake lines are specifically designed to endure extreme hydraulic pressure and temperature. Standard hoses may fail under similar stress. Always use manufacturer-recommended components for safety.
Q: What are signs of a failing high pressure brake hose?
A: Common signs include brake fluid leaks, spongy pedal feel, or visible cracks/swelling on the hose surface. Immediate replacement is necessary to prevent brake failure. Regular inspections are recommended.
Q: Are high pressure brake hoses compatible with all brake fluids?
A: Most are compatible with DOT 3, DOT 4, or DOT 5.1 fluids, but material compatibility varies. Check the hose specifications for fluid type restrictions. Using incorrect fluids can degrade rubber or synthetic linings.
Product Application