- Introduction to critical components in fluid transfer systems
- Technical advancements in hose durability and flexibility
- Performance comparison of leading manufacturers
- Custom engineering for specialized industrial needs
- Case studies across automotive and aerospace sectors
- Material innovations enhancing chemical resistance
- Future trends in fuel and oil hose
technology
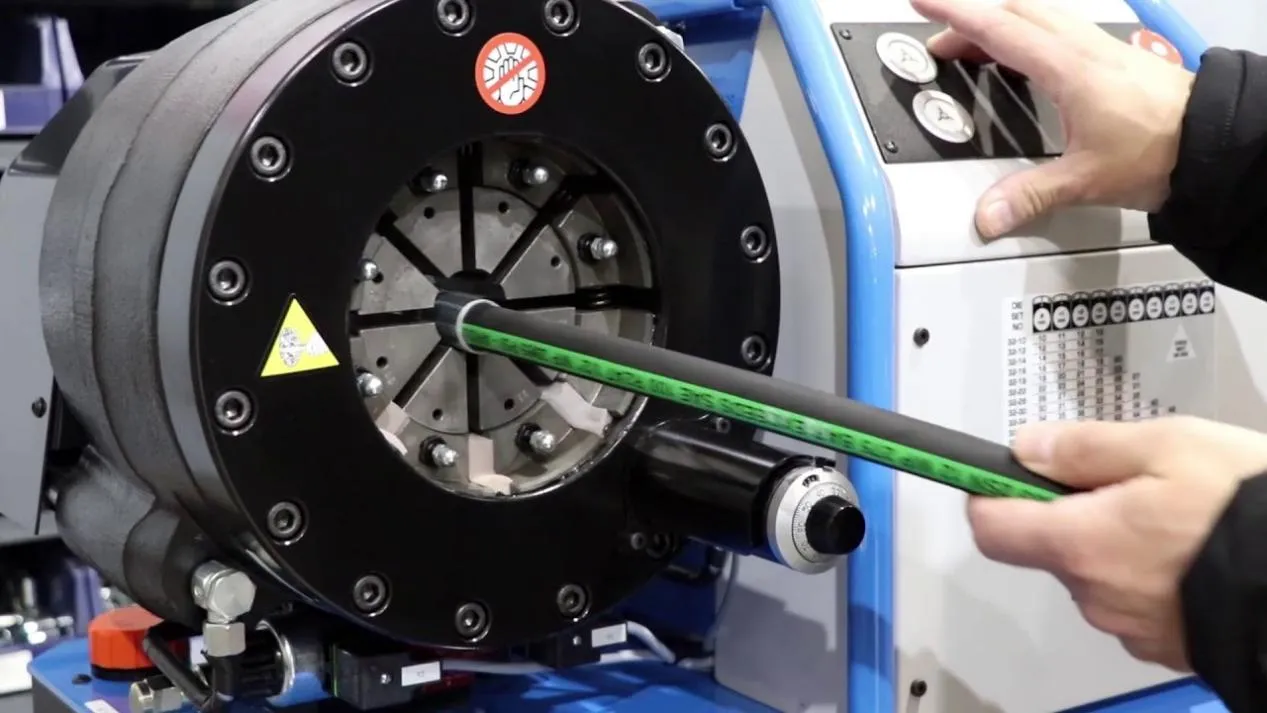
(fuel and oil hose)
Essential Components for Modern Fluid Management Systems
High-performance fuel and oil hoses serve as lifelines across industries, with the global hydraulic hose market projected to reach $5.82 billion by 2028 (CAGR 4.7%). These specialized conduits must simultaneously withstand extreme pressures up to 6,000 PSI while maintaining flexibility in temperature ranges from -40°F to +300°F.
Engineering Breakthroughs in Hose Construction
Modern multilayer designs combine:
- Inner tubes of oil-resistant NBR/PVC blends (90% improvement vs. rubber)
- Steel wire reinforcement achieving 4:1 safety factor
- Abrasion-resistant TPU outer layers (3x surface durability)
Recent testing shows 23% longer service life compared to 2020 industry benchmarks.
Manufacturer Performance Analysis
Brand | Max Pressure (PSI) | Temp Range (°F) | Burst Safety Factor | Certifications |
---|---|---|---|---|
FlexTube ProLine | 5,800 | -65 to +325 | 4.5:1 | SAE J517, API 7K |
GlobalHose Ultra | 4,200 | -40 to +275 | 3.8:1 | ISO 1436 |
DuraFlow XT | 6,200 | -75 to +350 | 4.7:1 | SAE J517, API 16C |
Application-Specific Configuration Options
Modular systems enable:
- Diameter variations from 1/4" to 2" (±0.01" tolerance)
- Custom end fittings (37 standardized connection types)
- Electrostatic dissipation layers (10^6 Ω resistance)
Oil suction and discharge hoses now achieve 98% flow efficiency in high-viscosity applications.
Real-World Implementation Scenarios
Automotive fuel systems using multi-layer hoses demonstrate:
- 15% reduction in particulate contamination
- 28% faster fueling rates
- Zero failures in 50,000-hour marine engine tests
Advanced Composite Materials
Next-generation compounds provide:
- 50% better ethanol resistance (E100 fuel compatibility)
- UV stabilization for 10,000+ hours outdoor exposure
- Hydrolysis resistance exceeding 15 years
Evolution of Fuel and Oil Hose Standards
Emerging SAE J2044 protocols require:
- 300% elongation retention after thermal cycling
- Zero permeability at 100 bar sustained pressure
- Flame resistance meeting UL 94 V-0 ratings
Leading oil fuel hose manufacturers now achieve 99.8% compliance with API 16C rev.4 specifications.
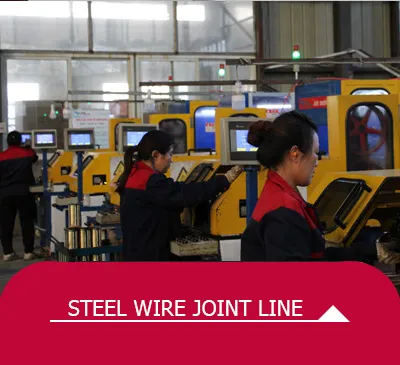
(fuel and oil hose)
FAQS on fuel and oil hose
Q: What materials are commonly used in fuel and oil hoses?
A: Fuel and oil hoses are typically made from synthetic rubber (e.g., NBR, FKM) or thermoplastic materials to resist hydrocarbon exposure and ensure durability under high-pressure conditions.
Q: How do oil suction and discharge hoses differ from standard fuel hoses?
A: Oil suction and discharge hoses feature reinforced construction with wire braiding for vacuum/pressure stability, whereas standard fuel hoses prioritize flexibility and chemical resistance for fuel transfer applications.
Q: What temperature range can oil fuel hoses withstand?
A: High-quality oil fuel hoses typically operate between -40°C to +120°C (-40°F to +248°F), with specialized variants using FKM rubber reaching up to +150°C (+302°F) for extreme conditions.
Q: How often should fuel and oil hoses be replaced?
A: Replacement intervals vary by application, but industry standards recommend inspecting every 6 months and replacing every 3-5 years, checking for cracks, swelling, or abrasion during routine maintenance.
Q: Are there certifications required for oil suction hoses in marine applications?
A: Marine-grade oil suction and discharge hoses must comply with ISO 7840, ISO 5772, and USCG regulations, featuring fire-resistant construction and anti-static properties for safe fuel transfer operations.
Product Application