The rubber hose manufacturing process is a fascinating fusion of art and science, involving meticulous engineering, innovative technology, and skilled craftsmanship. Its significance spans across various industries, including automotive, agriculture, oil and gas, and household applications. Here's an expert's view into this highly specialized process, breaking down its complex steps and highlighting the unique expertise required to create high-quality rubber hoses.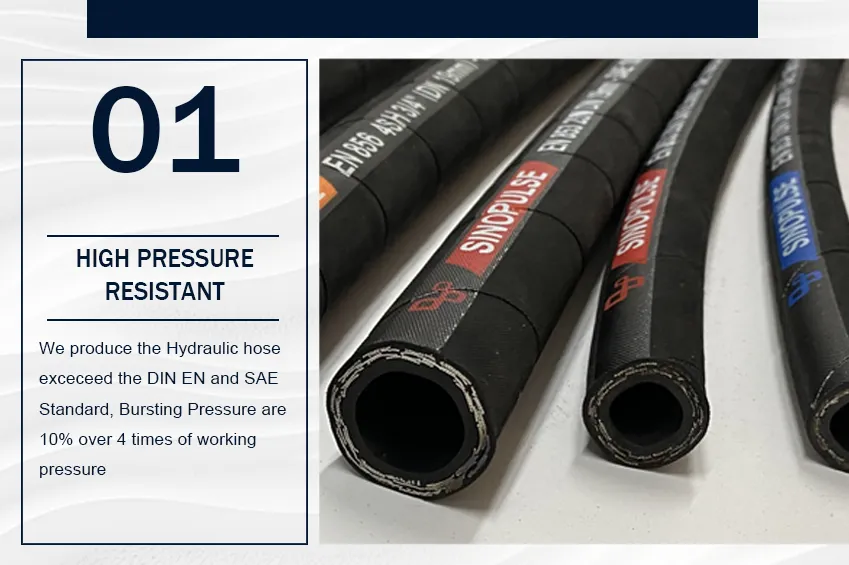
At the heart of rubber hose manufacturing is the formulation of rubber compounds. The process begins with the selection and mixing of raw materials, which typically include natural rubber, synthetic rubber, and various additives. This formulation is critical as it determines the hose's mechanical properties, chemical resistance, and flexibility. Experts in material science meticulously calculate and experiment to optimize these formulas, ensuring the final product meets rigorous industry standards.
Once the compound is prepared, the next crucial step is extrusion. This involves forcing the rubber compound through a die to create the desired hose shape. Advanced extrusion technology allows for precise control over dimensions and consistency, which is vital for ensuring that each hose performs reliably under pressure. The intricacies of extrusion require not only cutting-edge machinery but also experienced operators who understand the nuances of temperature control and flow dynamics.
Following extrusion, the hoses undergo vulcanization, a chemical process that enhances elasticity and strength. This stage involves heating the extruded rubber in the presence of sulfur, initiating a cross-linking reaction between rubber molecules. Vulcanization is a delicate procedure that demands expertise, as improper temperature or timing can compromise the hose's integrity. Industry veterans leverage their deep understanding of this process to ensure optimal vulcanization conditions.
In certain applications, additional reinforcement layers are essential for durability and performance. Braiding, spiraling, or knitting techniques are applied to weave reinforcing fibers into the hose structure. The choice of reinforcement method relies heavily on the intended application and environmental conditions that the hoses will be exposed to. Skilled engineers assess factors such as burst pressure and tensile strength to select the most appropriate reinforcement strategy.rubber hose manufacturing process
Quality control throughout the manufacturing process is paramount. Each hose undergoes rigorous testing to validate its performance characteristics, including pressure endurance, flexibility, and abrasion resistance. State-of-the-art diagnostic tools and real-world simulation tests are employed, facilitated by specialists proficient in quality assurance protocols. This process not only guarantees compliance with international standards but also builds customer trust and product reliability.
Innovation plays a key role in enhancing rubber hose manufacturing. Industry leaders invest in research and development to create hoses that push the boundaries of capability and efficiency. Recent advancements include the integration of nanomaterials to improve thermal stability and the use of eco-friendly additives to reduce environmental impact. The commitment to technological advancement reflects an industry deeply invested in sustainable progress.
Establishing a reputation for quality and reliability in the rubber hose manufacturing domain involves more than technical expertise; it requires a culture of accountability and continuous improvement. Leading manufacturers emphasize training and development, ensuring their workforce stays at the forefront of technological developments and best practices. This commitment to excellence cultivates trust and positions these companies as authoritative entities in the industry.
In conclusion, the rubber hose manufacturing process is a sophisticated blend of science, engineering, and practical know-how. Mastery over each stage—from material selection to final testing—demands a high level of expertise and innovation. With the continuous evolution of technology and materials, the industry is poised to address emerging challenges, fulfilling the ever-expanding need for high-quality, reliable hoses across various sectors.
OUR LATEST NEWS
Strict quality control strict production team to ensure stable products quality. Scientific personnel management, efficient production arrangements to ensure our timely delivery.