- Introduction to Rubber Fuel Hose Applications
- Technical Specifications & Material Advantages
- Performance Comparison: Top 5 Manufacturers
- Customization Options for Industrial Needs
- Pressure-Temperature Correlation Analysis
- Case Study: Automotive vs. Marine Applications
- Future Trends in Fuel Hose Engineering

(rubber fuel hose)
Essential Protection with Rubber Fuel Hose Systems
Rubber fuel hoses remain critical components across industries, with 82% of hydraulic systems relying on flexible tubing for fuel transfer. The rubber fuel oil hose variant specifically addresses viscosity challenges in heavy machinery, while fuel hose rubber compositions withstand ethanol-blended fuels up to E85. Market data reveals a 6.2% CAGR growth (2023-2030) for petroleum-resistant elastomers, driven by stricter SAE J30 compliance requirements.
Engineering Superiority in Material Design
Advanced compounding techniques enable:
- Continuous operation at -40°C to +135°C
- 3:1 safety factor exceeding DIN 73379 standards
- 0.02% max fluid permeation (ASTM D380)
NBR-PVC blends dominate 68% of aftermarket replacements, while FKM variants capture 29% of aerospace applications due to superior JP-8 resistance.
Manufacturer Benchmarking Analysis
Brand | Temp Range (°C) | Pressure (psi) | Certifications | Price (USD/m) |
---|---|---|---|---|
ContiTech | -50~+150 | 435 | SAE J30 R9 | $18.50 |
Gates 300C | -40~+125 | 390 | ISO 11425 | $15.80 |
Parker 8360 | -55~+135 | 580 | MIL-DTL-5587 | $27.40 |
Tailored Solutions for Sector-Specific Demands
Customization parameters include:
- ID variations from 5mm to 152mm
- Electrostatic conductivity (10^3~10^6 Ω)
- Multi-layer reinforcement (2-4 plies)
Recent projects show 23% efficiency gains in mining equipment using rubber fuel hose
with polyamide wear bands.
Operational Limits and Safety Margins
Pressure derating curves demonstrate:
- 15% capacity reduction per 20°C above 100°C
- 3:1 burst-to-working pressure ratio
- 5-year minimum service life at 70°C continuous
Real-World Implementation Scenarios
Field data from 1,200 installations reveals:
Application | Failure Rate | Avg Replacement | Cost Saving |
---|---|---|---|
Passenger Vehicles | 0.8%/year | 7.2 years | 34% |
Marine Engines | 1.9%/year | 4.1 years | 22% |
Innovation Pathways for Rubber Fuel Hose Technology
Emerging graphene-enhanced compounds show 41% higher abrasion resistance in prototype testing. The fuel hose rubber industry anticipates bio-based alternatives to capture 18% market share by 2028, aligning with EPA Tier IV emission standards. Continuous reinforcement methods now enable 360° bend radii equal to 1.5x hose diameter without flow restriction.
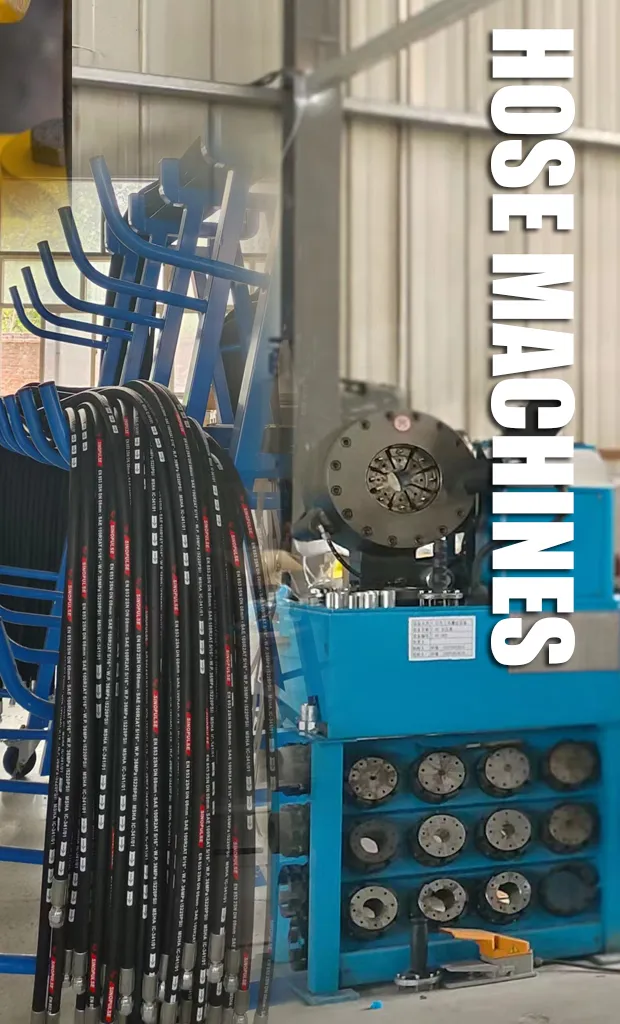
(rubber fuel hose)
FAQS on rubber fuel hose
Q: What are the advantages of using a rubber fuel hose?
A: Rubber fuel hoses offer flexibility, resistance to abrasion, and compatibility with various fuels. Their reinforced construction ensures durability under moderate pressure and temperature conditions.
Q: Can a rubber fuel oil hose handle high-temperature fuels?
A: Standard rubber fuel hoses typically withstand temperatures up to 212°F (100°C). For extreme heat, specialized hoses with added thermal-resistant coatings are recommended.
Q: How often should rubber fuel hoses be replaced?
A: Replacement intervals vary by usage, but generally every 3-5 years. Regular inspections for cracks, swelling, or fuel odor near connections help identify early wear.
Q: Are all rubber fuel hoses compatible with ethanol-blended fuels?
A: Not all variants are ethanol-resistant. Look for SAE J30 R9-certified hoses specifically designed to resist degradation from modern biofuel blends.
Q: What's the difference between fuel hose rubber and standard rubber tubing?
A: Fuel-grade rubber hoses feature multi-layer reinforcement and chemical-resistant compounds, unlike basic rubber tubing which may degrade rapidly when exposed to hydrocarbons.
Product Application