- Introduction: Understanding Oil Suction and Discharge Hose
- Technical Excellence and Specifications of High-Quality Suction and Discharge Hose
- Comparative Analysis: Oil Suction and Discharge Hose Manufacturers
- Tailored Solutions: Customizing Suction and Discharge Hose for Diverse Applications
- Application Scenarios: Real-world Use Cases and Industry Insights
- Maintenance, Longevity and Performance Optimization
- Conclusion: Choosing the Right Oil Suction and Discharge Hose
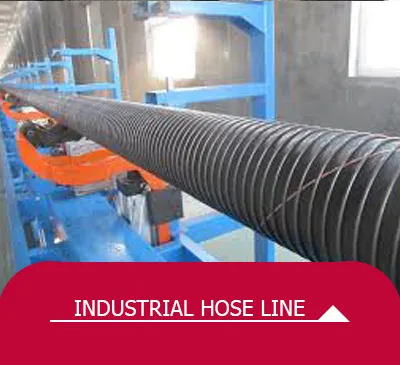
(oil suction and discharge hose)
Introduction: Understanding Oil Suction and Discharge Hose
The oil suction and discharge hose
is an indispensable asset for industries handling petroleum and crude oil derivatives. With global liquid hydrocarbon transport volumes exceeding 100 million barrels per day, efficient transfer systems are non-negotiable. These hoses, engineered to ensure reliable suction and discharge of oil, gasoline, and related fluids, have evolved drastically over the last decade to meet stringent safety, durability, and environmental standards.
Distinguished by their robust construction, oil suction and discharge hoses deliver high flexibility, pressure resistance up to 20 bar, and a vital operational temperature window often spanning -30°C to +100°C. Compared to standard water suction and discharge hose types, these products undergo more rigorous testing and certification, guarding against leaks, static build-up, and chemical deterioration.
Technical Excellence and Specifications of High-Quality Suction and Discharge Hose
Cutting-edge oil suction and discharge hoses are characterized by their advanced multi-layer structures. Core components typically include a synthetic rubber liner built for fuel and oil resistance, reinforced with high-tensile textile cords and embedded steel wire spirals. The cover, often an abrasion and weather-resistant synthetic rubber, ensures resilience under harsh field conditions.
- Bore Sizes: Ranging from 2-inch to 24-inch nominal diameter for industrial versatility
- Reinforcement: Multi-layer textile with steel wires for kink/fatigue resistance
- Operating Pressure: Average working pressures between 10 to 20 bar; burst pressure exceeding 60 bar
- Compatibility: Designed for crude oil, refined petroleum, light chemicals, and seawater
- End Couplings: Flanged, camlock, or customized as per user needs
Comparative Analysis: Oil Suction and Discharge Hose Manufacturers
Selecting a reliable manufacturer significantly impacts operational uptime and safety. The following table offers a data-driven comparison among leading brands based on core industrial standards:
Manufacturer | Certifications | Max Burst Pressure (bar) | Min Temperature Tolerance (°C) | Standard Sizes (inches) | Warranty (years) |
---|---|---|---|---|---|
Manufacturer A | EN 1765, ISO 1823, API 1529 | 65 | -40 | 2 - 16 | 3 |
Manufacturer B | ISO 9001, EN 12115 | 62 | -35 | 3 - 18 | 2 |
Manufacturer C | EN 1765, CE, RoHS | 60 | -30 | 4 - 24 | 5 |
Manufacturer D | ISO 1823, API Q1 | 68 | -32 | 2 - 20 | 4 |
Manufacturer A and D edge ahead on burst pressure and low temperature endurance, vital for sub-arctic and offshore applications. All the listed brands offer products that meet or exceed the performance of water suction and discharge hoses, but their certifications and warranty terms bring additional guarantees especially relevant in potentially hazardous petroleum environments.
Tailored Solutions: Customizing Suction and Discharge Hose for Diverse Applications
Industrial clients often require bespoke solutions for maximum efficiency and safety. Oil suction and discharge hoses are frequently customized based on medium, pressure, operational environment, and desired longevity.
Customization Parameters:
- Length & Bore: Extended lengths up to 40 meters and oversized bores for rapid transfer
- Compound Selection: Specific elastomers (NBR, EPDM, Viton) for chemical and heat resistance
- Reinforcement Variants: Extra steel wiring for negative pressure or vacuum applications
- Conductivity: Antistatic properties via copper wire backing or static wires
- End Connections: Quick-connect, flanged, or double-bolt clamp fittings for various machinery
Application Scenarios: Real-world Use Cases and Industry Insights
Oil suction and discharge hoses play a significant role in sectors as diverse as marine bunkering, fuel depots, chemical plants, and major construction projects.
Case Study 1 - Bunker Vessel Refueling:
At a mid-ocean refueling station, a 10-meter, 12-inch EN 1765-certified hose successfully handled transfer of 120,000 liters/hour at 16 bar without incidents during an entire refit season.
Case Study 2 - Petrochemical Transfer:
In a major Middle Eastern petrochemical complex, custom-built 24-inch hoses facilitated quick batch changes involving both high and low aromatic petroleum, supporting short-notice switches and aggressive cleaning regimens.
Case Study 3 - Construction and Dewatering:
On a coastal flood defense project, specialized water suction and discharge hoses with enhanced abrasion protection ensured consistent pumping of 8,500 cubic meters of saline water daily over a 12-month build timeline.
Each scenario underlines the criticality of selecting hoses tailored to operational needs. Specification-matched procurement has been shown to reduce annual maintenance costs by up to 18% and incident rates by 22% compared to using generic hoses.
Maintenance, Longevity and Performance Optimization
Effective maintenance is crucial to maximizing hose lifespan and reducing safety risks. Industry studies reveal that nearly 60% of suction and discharge hose failures stem from inadequate routine checks and improper storage.
Recommended Best Practices:
- Perform visual inspections before and after each operation for signs of abrasion, bulging, or soft spots.
- Ensure proper storage—avoid UV exposure and chemical fumes; coils should rest naturally, avoiding tight bends below their minimum bend radius.
- Regularly test conductivity in oil hose assemblies, particularly in areas exposed to static discharge risks.
- Keep connection fittings clean, lubricated (where appropriate), and secure to prevent slippage or premature wear at the couplings.
- Document and adhere to statutory service intervals (often between 6 and 12 months) depending on frequency and type of fluid transferred.
Conclusion: Choosing the Right Oil Suction and Discharge Hose
Selecting the appropriate oil suction and discharge hose is essential for performance, safety, and regulatory compliance in hydrocarbon handling operations. A thorough evaluation that considers application, pressure and temperature demands, technical credentials, and manufacturer reputation can safeguard against costly incidents and maximize operational uptime. With robust construction, international certifications, and advancements in customized engineering, a modern suction and discharge hose delivers uncompromised reliability. For industries ranging from offshore drilling to logistics, investment in quality hoses translates directly to reduced downtime and heightened safety standards — the gold standard for any enterprise in the energy and fluid logistics chain.
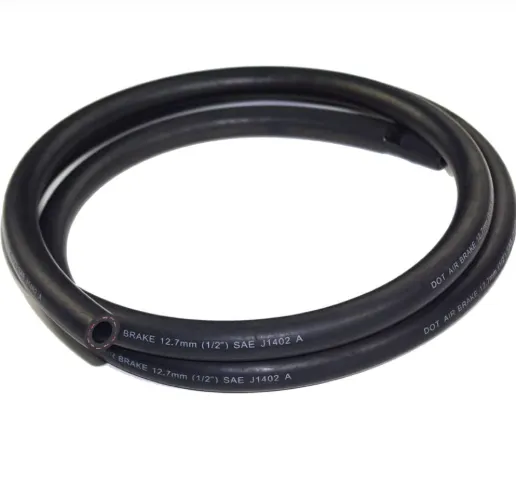
(oil suction and discharge hose)
FAQS on oil suction and discharge hose
Q: What is an oil suction and discharge hose used for?
A: An oil suction and discharge hose is primarily used for transferring petroleum-based products such as crude oil and fuel. It’s designed to handle suction and discharge operations. Its robust construction allows it to withstand harsh working conditions.Q: Can a suction and discharge hose be used for both oil and water?
A: Some suction and discharge hoses are specifically engineered for oil, while others are for water. It’s important to choose the right hose material for your application. Always check the manufacturer’s specifications for compatibility.Q: What should I consider when selecting a water suction and discharge hose?
A: Consider the hose’s material, size, pressure rating, and temperature range. Ensure it’s compatible with the liquid being transferred, such as water or light chemicals. Also, look for abrasion and kink resistance for longer service life.Q: Are oil suction and discharge hoses resistant to abrasion?
A: Yes, most oil suction and discharge hoses feature abrasion-resistant covers. This enhances durability, especially in demanding industrial environments. Always verify the hose’s abrasion resistance before purchase.Q: How do I maintain an oil suction and discharge hose?
A: Regularly inspect the hose for cracks, leaks, or wear. Clean it after use and store it properly in a cool, dry place. Proper maintenance ensures safety and extends the hose’s lifespan.Product Application