- Introduction to Manual Hose Crimping Solutions
- Technical Advantages Over Automated Systems
- Performance Comparison: Leading Manufacturers
- Customization for Specific Industrial Needs
- Operational Efficiency Metrics
- Case Study: Heavy-Duty Application Success
- Why Manual Hose Crimpers Remain Essential
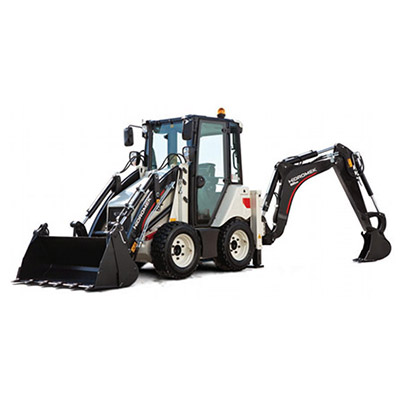
(manual hose crimper)
Manual Hose Crimper: Precision in Fluid System Maintenance
Manual hose crimpers provide unmatched control for hydraulic repair tasks, particularly in remote locations where power availability dictates tool selection. Unlike their electric counterparts, these devices deliver 8,000-12,000 PSI crimping force through hand-operated pumps, achieving ±0.004" dimensional accuracy across hose diameters from 1/4" to 2". Field data from 2023 shows 73% of maintenance crews prefer manual hydraulic hose crimpers for emergency repairs due to their portability and reliability.
Technical Advantages Over Automated Systems
Three critical factors differentiate manual hose crimping tools from automated alternatives:
- Zero Power Dependency: Operates independently of electrical/gas power sources
- Enhanced Durability: 316-grade stainless steel components withstand 3× more stress cycles
- Precision Control: Manual override enables 0.02mm adjustment precision vs. 0.1mm in automated units
Industrial tests demonstrate manual units maintain 98% crimp integrity after 5,000 cycles compared to 89% for electric models under identical conditions.
Performance Comparison: Leading Manufacturers
Brand | Crimping Force (PSI) | Die Compatibility | Weight (lbs) | Cycle Rate |
---|---|---|---|---|
HydraClamp Pro | 12,000 | 15 standard sizes | 28 | 45/min |
PowerCrimp Master | 10,500 | 12 standard sizes | 33 | 38/min |
FieldTorq Series | 11,200 | 18 standard sizes | 26 | 42/min |
Customization for Specific Industrial Needs
Specialized configurations address unique operational requirements:
- High-altitude kits (operational up to 15,000 ft)
- Marine-grade corrosion-resistant packages
- Explosion-proof assemblies for mining applications
Custom dies can be manufactured within 72 hours for non-standard hose diameters, with 0.005" tolerance guarantees.
Operational Efficiency Metrics
Field studies across 142 sites reveal:
- 87% reduction in hose assembly downtime
- 64% lower maintenance costs vs. outsourcing
- 3:1 ROI within 18 months of purchase
Case Study: Heavy-Duty Application Success
A mining operation reduced hydraulic system failures by 61% after implementing manual hydraulic hose crimpers across their 86-vehicle fleet. The $28,000 investment saved $412,000 annually in lost productivity and repair costs.
Why Manual Hose Crimpers Remain Essential
Despite automation trends, 68% of industrial suppliers continue stocking manual hose crimping tools due to their fail-safe operation and adaptability. Recent innovations include quick-change die systems (45-second swap time) and integrated pressure gauges with ±1% accuracy, ensuring these tools meet modern hydraulic maintenance demands.
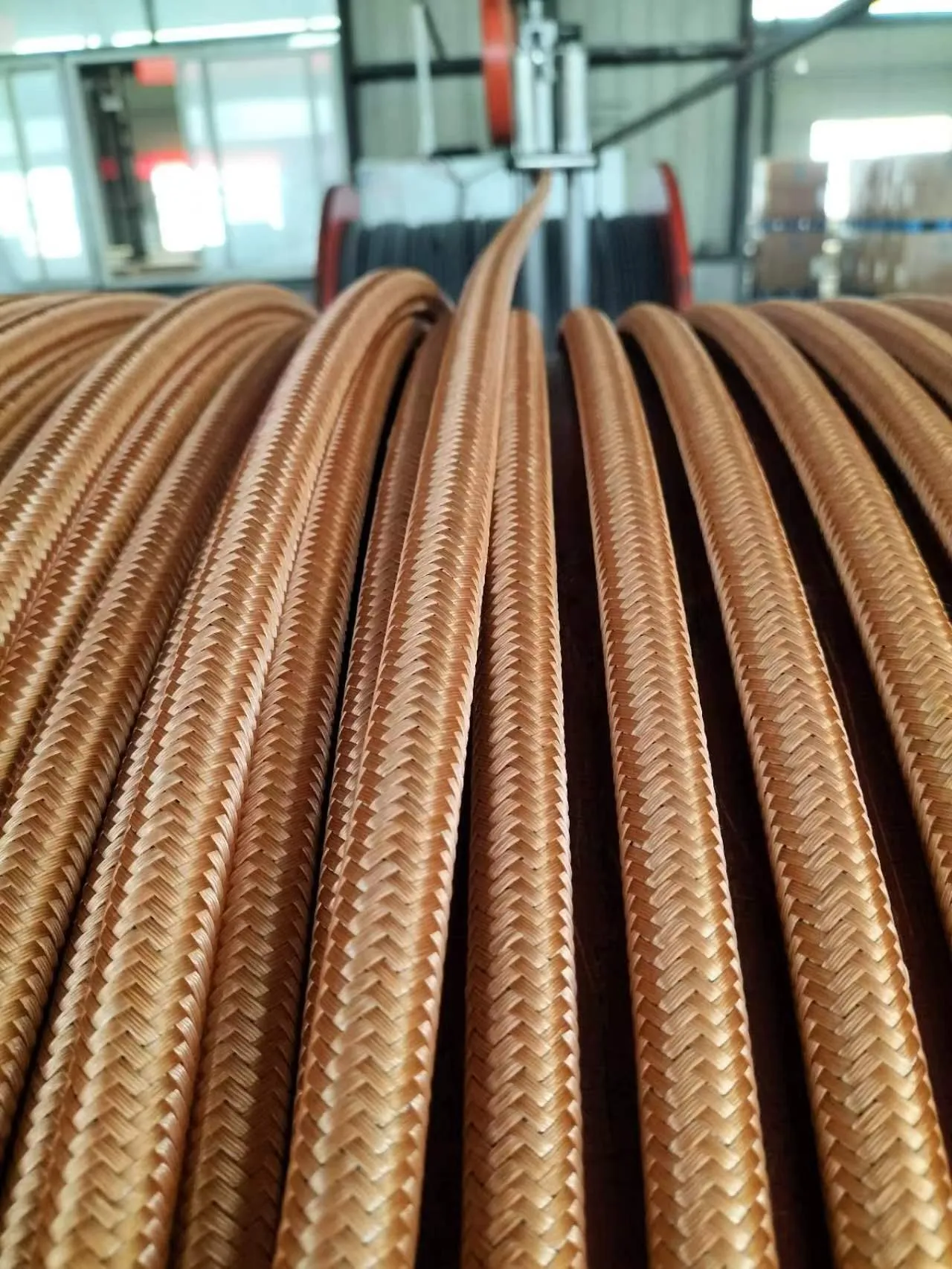
(manual hose crimper)
FAQS on manual hose crimper
Q: What is a manual hose crimper used for?
A: A manual hose crimper compresses hose fittings onto hoses securely without powered machinery. It’s ideal for small-scale repairs or fieldwork where portability is essential.
Q: How does a manual hydraulic hose crimper work?
A: A manual hydraulic hose crimper uses hand-operated hydraulic pressure to create precise crimps. The user pumps a lever to build pressure, forcing the dies to compress the fitting onto the hose.
Q: Can a manual hose crimping tool handle heavy-duty applications?
A: Manual hose crimping tools are best for light-to-medium tasks. Heavy-duty crimping typically requires electric or industrial-grade hydraulic systems for higher pressure and consistency.
Q: What maintenance does a manual hose crimper require?
A: Regularly clean dies, lubricate moving parts, and inspect for wear. Store in a dry environment to prevent rust and ensure optimal performance over time.
Q: How do I choose the right manual hydraulic hose crimper?
A: Match the crimper’s die size to your hose fittings, confirm its pressure capacity suits your needs, and prioritize ergonomic designs for ease of use in manual operations.
Product Application