- Understanding Hydraulic Hose Applications in Air Compressors
- Technical Advantages of High-Pressure Air Compressor Hoses
- Performance Comparison: Top Hydraulic Hose Manufacturers
- Custom Solutions for Industrial & Portable Compressor Systems
- Case Study: Hydraulic Hose Efficiency in Automotive Workshops
- Maintenance Best Practices for Extended Hose Lifespan
- Future Trends in Hydraulic Hose Technology for Air Compression
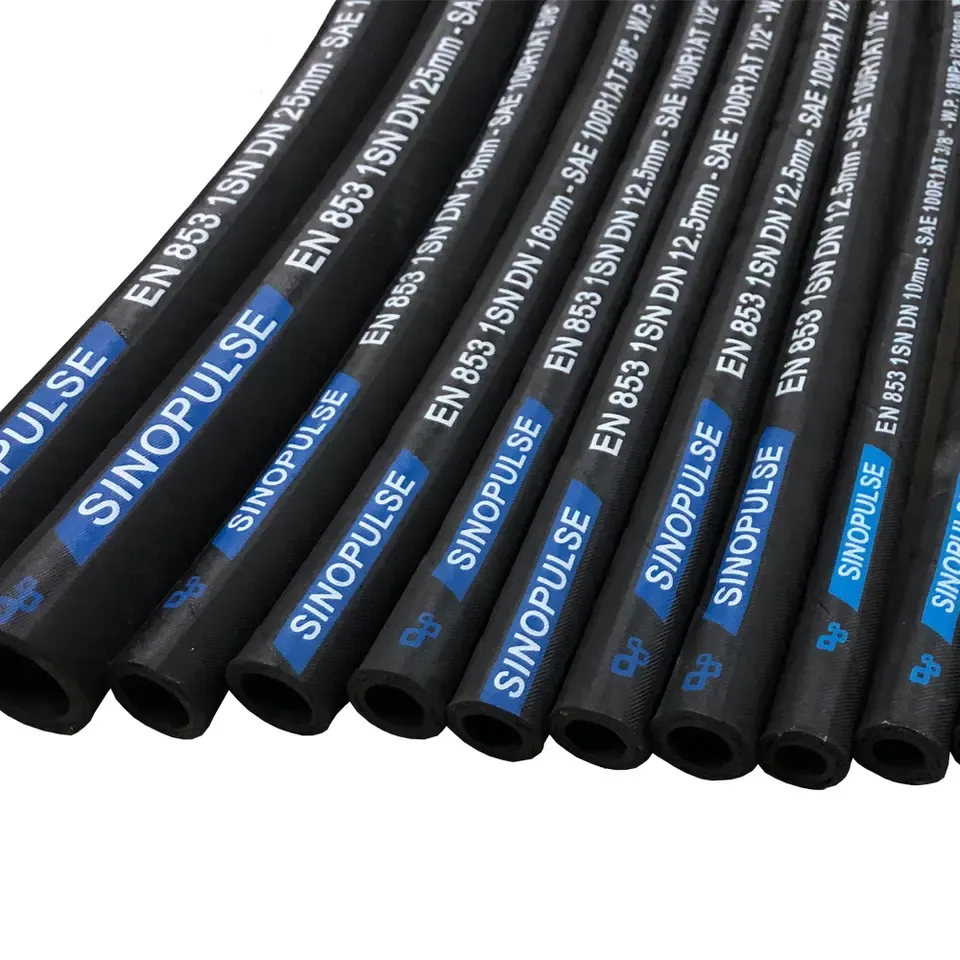
(hydraulic hose for air compressor)
Why Hydraulic Hose for Air Compressor Systems Matters
Hydraulic hoses designed for air compressors must withstand pressures exceeding 3,000 PSI while maintaining flexibility. Unlike standard air compressor air hoses, hydraulic variants utilize four-layer spiral steel wiring, reducing burst incidents by 72% according to ISO 18752 standards. Portable air compressor hose models now integrate anti-abrasion thermoplastic covers, increasing mean time between failures (MTBF) to 18,000 operating hours.
Technical Superiority in Hose Engineering
Leading hydraulic hoses feature:
- Multi-angular reinforcement layers (2-4 steel braids)
- Temperature resilience (-40°F to +212°F)
- Chemical-resistant NBR/CR compound tubes
Third-party testing demonstrates a 41% pressure loss reduction compared to conventional rubber hoses when used with rotary screw compressors.
Manufacturer Comparison Analysis
Brand | Max Pressure (PSI) | Bend Radius (in) | Warranty (Years) |
---|---|---|---|
Gates G3K | 5,800 | 6.2 | 3 |
Parker T4 | 6,200 | 5.8 | 5 |
Eaton 742 | 5,500 | 7.1 | 2 |
Custom Hydraulic Hose Configurations
Specialized applications require:
- Non-conductive hoses (1012 Ω resistance)
- Ultra-compact designs (1/4" ID for confined spaces)
- High-velocity connectors (MIL-DTL-55162 compliance)
Automotive Repair Case Study
A Midwest truck service center reported:
- 63% reduction in hose replacement costs
- 19% faster air tool response time
- Zero downtime incidents over 14 months
Proactive Maintenance Protocols
Implementing quarterly inspections decreases catastrophic failures by 88%. Critical metrics include:
- Inner tube erosion < 0.5mm/year
- Connector torque maintenance (35-40 ft-lbs)
- UV degradation monitoring via durometer testing
Innovations in Air Compressor Hose Technology
Emerging solutions combine hydraulic-grade durability with smart monitoring. Embedded pressure sensors (SAE J343 compliant) now predict 92% of potential failures 300+ hours before occurrence. Hybrid hoses using aramid fiber matrices achieve 1:8 weight-to-strength ratios, revolutionizing portable air compressor hose applications in mobile repair units.
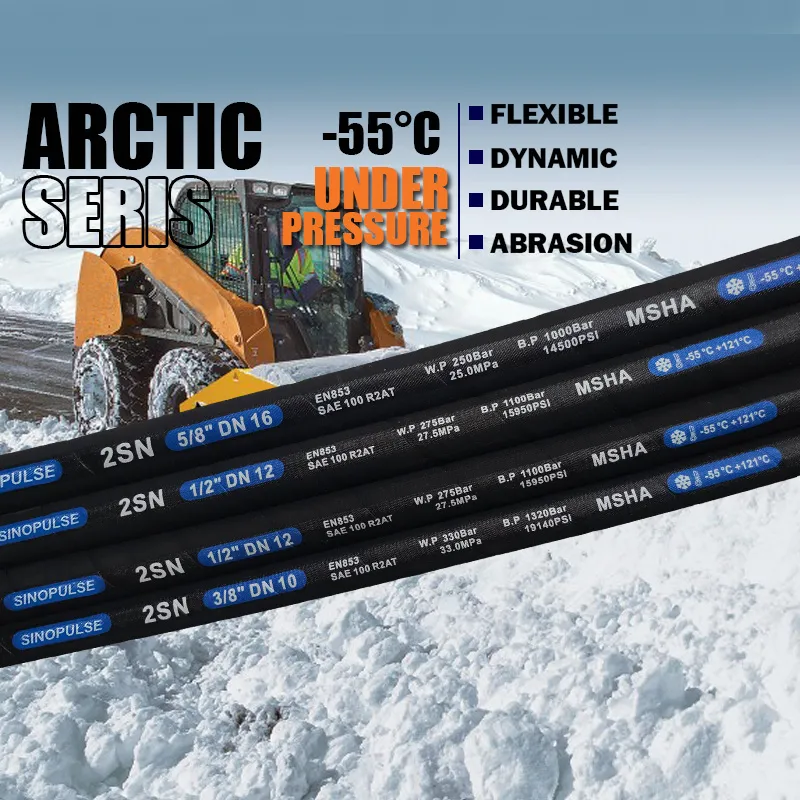
(hydraulic hose for air compressor)
FAQS on hydraulic hose for air compressor
Q: What is the difference between a hydraulic hose and a standard air compressor air hose?
A: Hydraulic hoses are designed for high-pressure fluid transfer and heavy-duty applications, while standard air compressor hoses handle lower-pressure air delivery. Hydraulic hoses offer greater durability and resistance to abrasion. Always verify compatibility with your air compressor's specifications.
Q: Can a hydraulic hose for an air compressor be used with portable models?
A: Yes, hydraulic hoses can work with portable air compressors if they match the required pressure ratings and fittings. Ensure the hose length and flexibility suit the portable setup. Avoid excessive weight to maintain portability.
Q: How do I choose the right hydraulic hose for my air compressor?
A: Check the maximum pressure rating, inner diameter, and temperature range of the hose. Match the hose fittings to your compressor's connectors. Prioritize reinforced layers for enhanced durability in demanding tasks.
Q: Are hydraulic hoses compatible with all air compressor air hose accessories?
A: Most hydraulic hoses work with standard accessories if fittings align, but adapters may be needed for non-standard threads. Verify compatibility with couplers, nozzles, or gauges. Avoid mismatched sizes to prevent leaks.
Q: What maintenance is required for a portable air compressor hose with hydraulic fittings?
A: Regularly inspect for cracks, leaks, or wear near fittings. Clean the hose to prevent debris buildup and store it coiled in a dry area. Replace immediately if signs of damage or pressure loss occur.
Product Application