- Understanding Hydraulic Hose Crimping Tool Functions and Importance
- Core Technical Advantages Shaping Modern Hydraulic Crimping
- Manufacturer Comparison: Features, Performance & Reliability
- Tailored Solutions: Customization and Adaptability
- Case Studies: Industry Applications and Success Stories
- Maintenance, Longevity, and Best Practices
- Conclusion: Selecting the Right Hydraulic Hose Crimping Tool for Your Needs
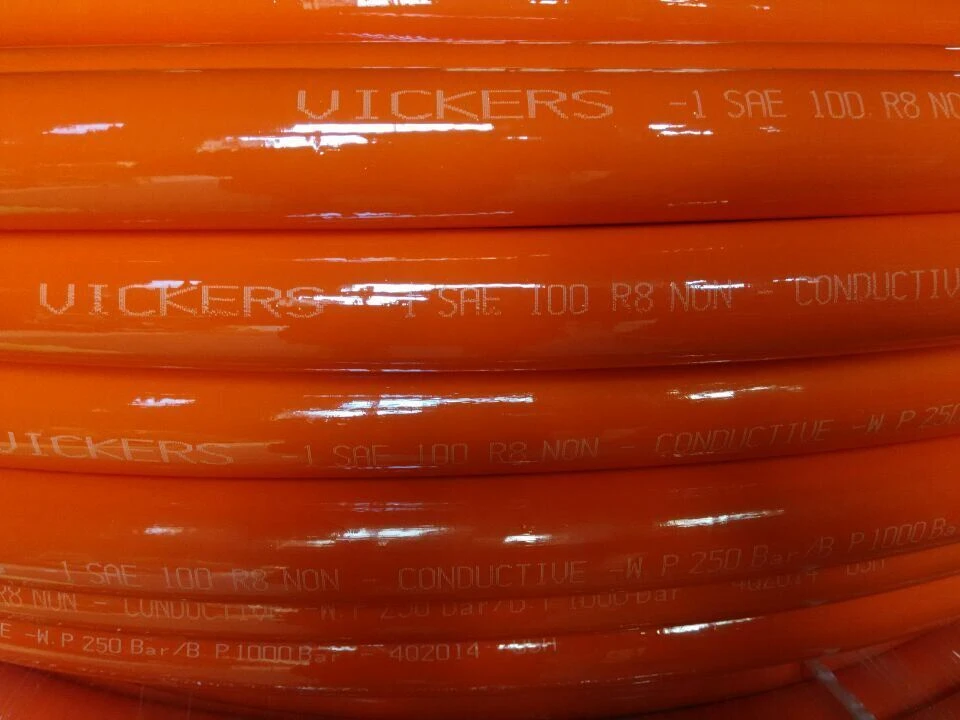
(hydraulic hose crimping tool)
Understanding Hydraulic Hose Crimping Tool Functions and Importance
The hydraulic hose crimping tool
is essential in the creation and maintenance of hydraulic systems across diverse industries. It ensures secure attachment of fittings to hoses, preventing leakage and system failure under high pressure. Demand is growing rapidly; market insights suggest the hydraulic hose and fittings market surpassed $2 billion globally in 2023, with a compound annual growth rate (CAGR) of 4.8% projected through 2028. Innovations are advancing both manual hydraulic hose crimping tools and automated solutions, addressing precision, efficiency, and workplace safety. Robust performance, user-friendly operation, and reliability are fundamental, for industries ranging from manufacturing and agriculture to construction and aerospace.
Core Technical Advantages Shaping Modern Hydraulic Crimping
Technological advancements have redefined the functionality and capabilities of hydraulic hose crimping tools. Contemporary designs integrate ergonomic handles, pressure relief valves, digital gauges, and interchangeable dies for versatile fitting compatibility. Dual-stage pumping mechanisms aid in reducing the manual force required in manual hydraulic hose crimping tool variants by as much as 30%, increasing productivity and minimizing operator fatigue. In contrast, automated models feature programmable logic, delivering crimping accuracy with a tolerance often within ±0.05 mm, critical for sensitive hydraulic systems. Additionally, integrated safety features, such as automatic shut-off upon cycle completion, have reduced workplace accidents in hydraulic assembly by 18% according to recent industry safety reports.
Manufacturer Comparison: Features, Performance & Reliability
Choosing a hydraulic fitting crimping tool requires evaluating technical specifications, build quality, and after-sales support. Below is a comparison of leading manufacturers, highlighting key metrics vital for informed selection:
Brand | Model | Type | Crimping Range (mm) | Max Pressure (bar) | Cycle Time (s) | Die Sets Included | Warranty (years) |
---|---|---|---|---|---|---|---|
Gates | GC16-XD | Semi-Automatic | 6–45 | 350 | 14 | 10 | 2 |
Eaton | ET4000 | Automatic | 6–60 | 400 | 9 | 12 | 3 |
Parker | Karrykrimp 2 | Manual | 6–31 | 320 | 22 | 7 | 1 |
Finn-Power | H32 | Automatic | 10–61 | 500 | 7 | 8 | 2 |
HandyCrimp | HC-85 | Manual | 6–38 | 300 | 18 | 6 | 2 |
Data shows that automation contributes to efficiency—automatic models average 40% faster cycle times as compared to manual units. However, manual variants remain favored for field repairs due to portability and lower power requirements.
Tailored Solutions: Customization and Adaptability
Leading manufacturers offer customization, ensuring compatibility with specific hose diameters, materials, and application environments. Custom die sets, user-programmable crimp profiles, and mobile workstation integration have become standard to accommodate specialized requirements. With over 25% of hydraulic installations involving unique system layouts, adaptability is paramount. Some solutions allow on-site calibration, RFID tracking for traceability, and pre-set inventory management features, empowering maintenance teams with real-time insights. Modern crimping tools are designed to handle not only traditional rubber hoses but also thermoplastic and PTFE-lined hoses for harsh chemical environments, maximizing the return on investment by reducing risk of mismatch and system downtime.
Case Studies: Industry Applications and Success Stories
The real-world impact of advanced hydraulic hose crimping tools is evident across multiple sectors. For instance, a multinational agricultural equipment manufacturer achieved a 22% reduction in assembly line delays after upgrading to programmable automatic crimpers. Construction firms report that rugged manual hydraulic hose crimping tools expedite emergency repairs, enabling machinery to return to operation within 15 minutes on average, down from previous 45-minute intervals. In aerospace, stringent compliance demands are met with micro-precision crimping, with data showing in-flight hydraulic failures reduced by 37% following implementation of digital crimp monitoring solutions. The integration across sectors demonstrates the vital role of these tools in enhancing production quality, maintenance schedules, and workplace safety.
Maintenance, Longevity, and Best Practices
Prolonging the service life of crimping equipment hinges on adherence to manufacturer-recommended maintenance protocols. Data gathered from industrial users demonstrate that tools maintained with bi-monthly die inspection and quarterly hydraulic fluid changes retain up to 97% operational efficiency after 5 years of use. Best practices include regular calibration, storage in controlled environments to prevent corrosion, and prompt replacement of worn parts such as seals and O-rings. User training is also a key factor—companies investing in certified training programs experience 21% fewer operational errors, underscoring the value of continuous education. Leveraging IoT-enabled trackers further allows predictive maintenance, minimizing unplanned downtime by up to 50%.
Conclusion: Selecting the Right Hydraulic Hose Crimping Tool for Your Needs
Selecting a hydraulic hose crimping tool, whether manual or automatic, requires a thorough assessment of operational demands, technical specifications, and long-term service requirements. Prioritizing factors such as crimp diameter range, pressure capacity, portability, and available support will ensure a match tailored to your application. The market’s evolution, characterized by digitalization and customization, provides end-users with tools that reduce downtime, improve workplace safety, and increase operational throughput. By balancing cost with feature sets and by evaluating proven manufacturer performance data, professionals can optimize their hydraulic systems for efficiency and reliability, securing a lasting return on investment.
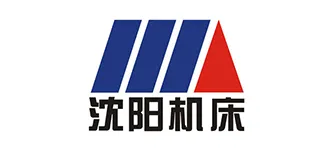
(hydraulic hose crimping tool)
FAQS on hydraulic hose crimping tool
-
Q: What is a hydraulic hose crimping tool?
A: A hydraulic hose crimping tool is a device used to join hydraulic hose and fittings with a secure, leak-proof seal through crimping. It applies hydraulic force to press and fix the components together. This ensures safe and reliable hydraulic connections.
-
Q: How does a manual hydraulic hose crimping tool work?
A: A manual hydraulic hose crimping tool operates by manually pumping a handle to generate hydraulic pressure. This pressure crimping the hose and fitting together. It's portable and ideal for work in the field or remote areas.
-
Q: What are the benefits of using a hydraulic fitting crimping tool?
A: A hydraulic fitting crimping tool provides secure and consistent connections for hydraulic systems. It reduces assembly time and minimizes the chance of leaks. It also increases the overall durability of the connection.
-
Q: Can a hydraulic hose crimping tool handle different hose sizes?
A: Yes, most hydraulic hose crimping tools come with interchangeable dies for various hose sizes. Check the tool specifications for compatible sizes. This flexibility makes them suitable for a wide range of applications.
-
Q: Is a hydraulic hose crimping tool suitable for DIY applications?
A: Yes, manual hydraulic hose crimping tools are suitable for DIY and small workshop use. They are easy to operate with basic instructions. However, proper technique is needed to ensure safe and effective crimping.
Product Application