Hose welding may seem like a straightforward task, but achieving a high-quality weld requires understanding and expertise. The domain of hose welding includes various techniques ensuring strong, reliable joints that stand the test of time and pressure. This article delves deeply into the critical aspects of hose welding, emphasizing authentic experiences and the expertise necessary for achieving optimal results.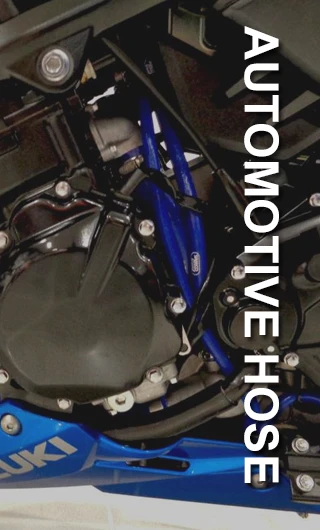
Understanding Hose Welding
Hose welding is not just about fusing two materials together; it is an intricate process that demands precision and an understanding of the materials being joined. Whether dealing with thermoplastic hoses or rubber ones, each requires a unique approach to welding. Notably, the welding process must account for the intrinsic elasticity and thermal properties of the materials.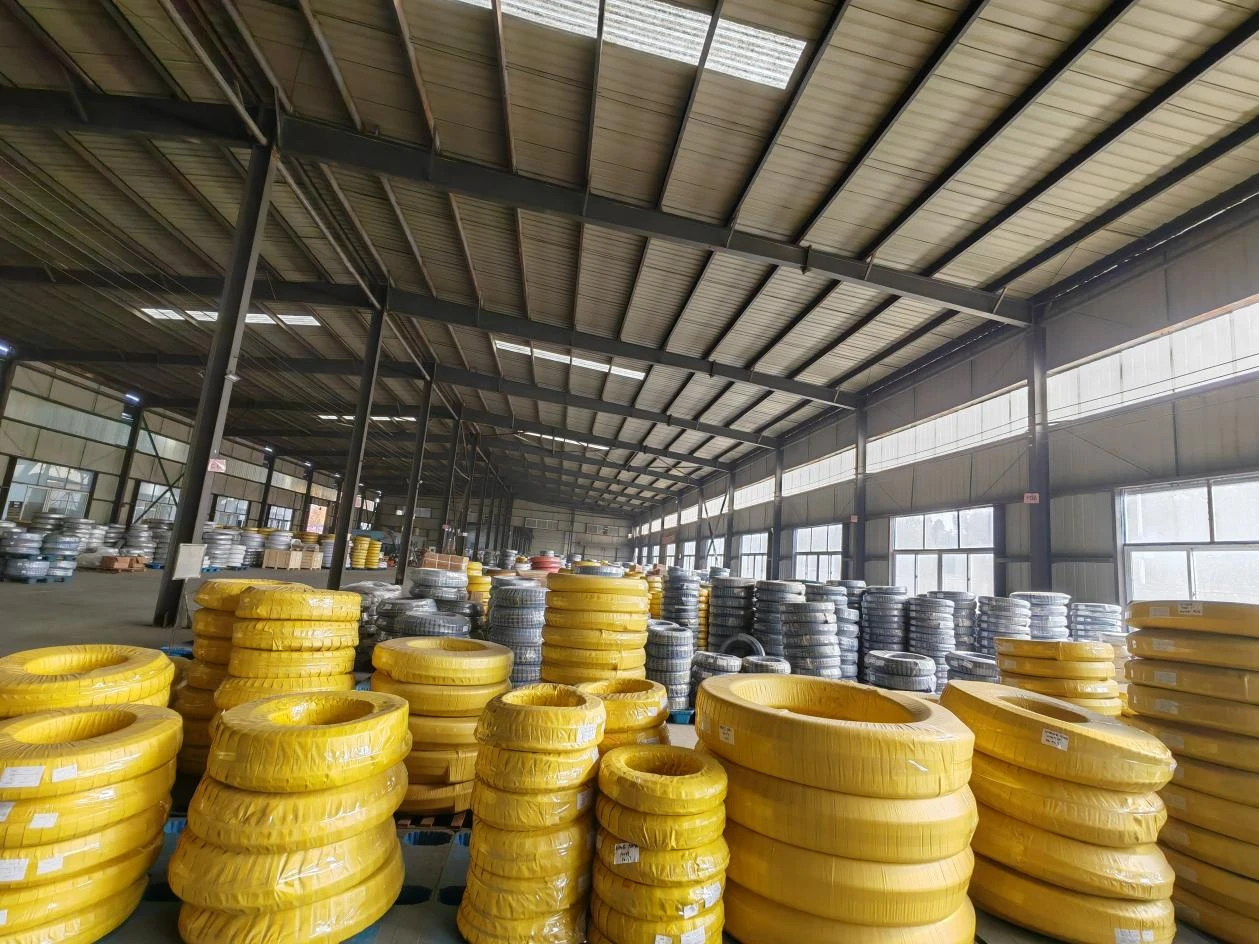
An early challenge in hose welding is selecting the correct welding technique. For thermoplastic hoses, methods such as hot-air welding or ultrasonic welding are prevalent due to their ability to precisely control heat application and create even joints that can withstand substantial stress. Rubber hoses, on the other hand, often require vulcanization or thermal welding to achieve a strong bond.
Expert Practices in Hose Welding
Achieving expertise in hose welding starts with proper training and hands-on experience. Those involved in welding must have a comprehensive understanding of the equipment, materials, and techniques available. Key to this is an understanding of heat control. Applying the right amount of heat is crucial; too much can degrade the hose material, while insufficient heat will result in a weak joint.
Safety is paramount in the practice of hose welding. Operators must adhere to rigorous safety protocols, including wearing protective gear and ensuring the welding environment is free from hazards. Precision tools and devices such as welding guns, heat lamps, and pressure rollers must be diligently maintained and calibrated to ensure they function correctly.
For those stepping into the field of hose welding, apprentice programs with established professionals offer invaluable opportunities to learn the nuances of the trade. These programs provide real-world scenarios that help in understanding various challenges such as handling different hose types or working in diverse environmental conditions.
Building Authoritativeness in Hose Welding
Developing a reputation as an authoritative figure in hose welding comes from continuous learning and adaptation to technological advancements. Attending workshops, seminars, and industry conferences enables professionals to stay updated on new welding technologies and methods. Furthermore, engaging in collaborative projects with industry-leading companies can bolster one's credentials and expand expertise.hose welding
Documentation and sharing of knowledge is another pathway to authoritativeness. Publishing research papers, articles, and guides on hose welding can establish a professional as a thought leader in the industry. Likewise, developing training modules and educational content for budding welders contributes to a legacy of expertise and credibility.
Trustworthiness in Hose Welding
Trustworthiness is the bedrock of a successful career in hose welding. Clients and collaborators should have confidence in a welder's ability to deliver high-quality, long-lasting results. This trust is built through transparency, communication, and by consistently producing work that meets or exceeds industry standards.
Establishing a transparent line of communication with clients about what they can expect regarding weld quality, timelines, and potential challenges is crucial. Regular feedback loops and project updates help in managing expectations and building strong, trusting relationships.
In terms of product reliability, using reputable equipment and materials is essential, and ensuring every weld undergoes rigorous quality testing aligns with maintaining high trust levels. Clients should be informed about the specific tests conducted and the standards complied with, such as pressure testing or tensile strength evaluations.
Continuous Evolution and Future Prospects
Hose welding, like many trades, continues to evolve with technological advancements. The advent of smart welding systems, which utilize digital interfaces and automated controls, promises to enhance precision and efficiency. Staying abreast of these changes and incorporating modern solutions into traditional welding practices will be crucial for future success.
To remain at the forefront of the hose welding industry, professionals must be proactive learners, adapting to both new challenges and technological advancements. By embodying the principles of expertise, authoritativeness, and trustworthiness, hose welders can not only advance their careers but also contribute significantly to the industry's growth and innovation.
In summary, hose welding is an art and a science requiring thorough understanding and skill. By focusing on continuous education, safety, and effective communication, welders can deliver exceptional quality work, earning the respect and trust of peers and clients alike.
OUR LATEST NEWS
Strict quality control strict production team to ensure stable products quality. Scientific personnel management, efficient production arrangements to ensure our timely delivery.