Understanding hose abrasion and its implications on industrial operations is crucial for ensuring safety and efficiency. Hose abrasion, often an overlooked issue, refers to the wearing down of hose material due to frictional contact with other surfaces or elements. Recognizing this, we must delve into the causes, impacts, preventive strategies, and the expert guidelines needed to maintain hose integrity.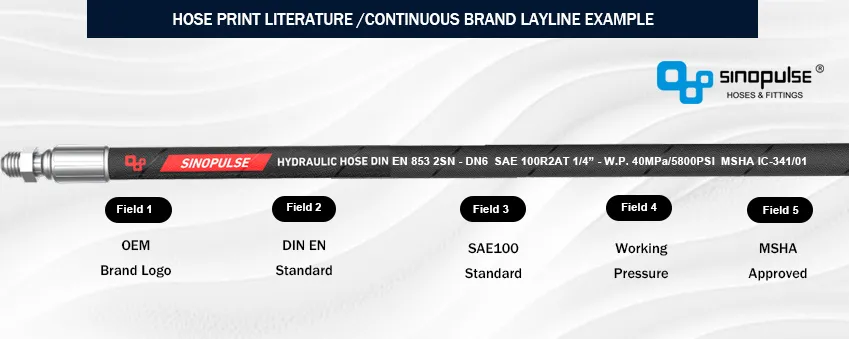
Industrial hoses are subjected to harsh environments and rigorous usage, making them vulnerable to abrasion. This wear and tear can come from external sources such as dragging across rough surfaces, rubbing against machinery, or internal causes like particles flowing through the hose at high velocities. The materials from which hoses are made, including rubber, polyurethane, and PVC, have varying degrees of resistance to abrasion. However, even the most robust materials can wear down without proper handling and maintenance.
The impact of hose abrasion isn't just about the physical degradation of the hose but extends to safety hazards and financial implications. A compromised hose can lead to fluid leaks, resulting in environmental contamination or accidents in the workplace. Furthermore, frequent replacements of abraded hoses can lead to increased costs and downtime, affecting overall productivity.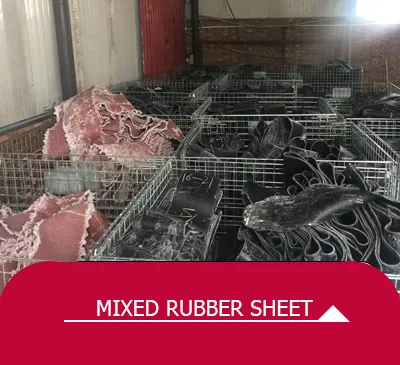
Addressing hose abrasion requires a multifaceted approach, integrating expert insights and practical solutions. Choosing the right material is paramount; for instance, hoses made with reinforced layers or specialized coatings can offer enhanced resistance. Additionally, routing hoses properly to minimize unnecessary contact with abrasive surfaces and implementing hose guards or protective sleeves can significantly reduce abrasion. Regular inspections and maintenance routines help in early detection of wear, preventing unexpected failures.
Incorporating personal experiences, one user from a prominent logistics firm shared how their team reduced downtime by 30% by implementing a combination of reinforced hose materials and protective coverings. This proactive approach not only extended the lifespan of their hoses but also improved safety by minimizing potential leaks.
Consulting with experts in hose manufacturing can provide valuable insights into selecting the right type of hose for specific environments. For instance, engineers can analyze the specific stress factors a hose will face and recommend products with greater durability and resilience. Authority in this field isn't just about having technical knowledge, but also understanding operational nuances and customer-specific challenges.hose abrasion
Dependability on trusted suppliers who prioritize quality and compliance can augment the trustworthiness of these solutions. A supplier’s commitment to rigorous testing and certification ensures that their hoses meet the necessary safety standards, providing peace of mind and reliability in high-stakes industrial settings.
Investing in technology for hose monitoring is another progressive solution. Utilizing smart technologies, like sensors and IoT devices, can help track wear in real-time, offering predictive maintenance capabilities. These innovations not only prevent abrasion-related downtimes but also align with modern industrial trends towards automation and smarter asset management.
The real crux of resolving hose abrasion is not only a technical endeavor but also a strategic approach, incorporating comprehensive knowledge, authoritative guidance, and trustworthy partnerships. Companies that prioritize these aspects in their operational frameworks tend to achieve better results, both in efficiency and safety.
Maintaining a balance between cost and quality is critical. While opting for high-quality abrasion-resistant hoses might seem initially expensive, the long-term gains in safety, efficiency, and reduced replacement frequency render it a sound investment. This reflects a broader understanding among industry leaders of the need for sustainable practices and solutions.
In conclusion, hose abrasion, while a common challenge, can be effectively mitigated with informed decisions based on expert advice and experience-backed strategies. By prioritizing materials, routine checks, expert consultations, and advanced technology, industries can enhance their operational reliability and safety, establishing themselves as frontrunners in maintaining best practices.
OUR LATEST NEWS
Strict quality control strict production team to ensure stable products quality. Scientific personnel management, efficient production arrangements to ensure our timely delivery.