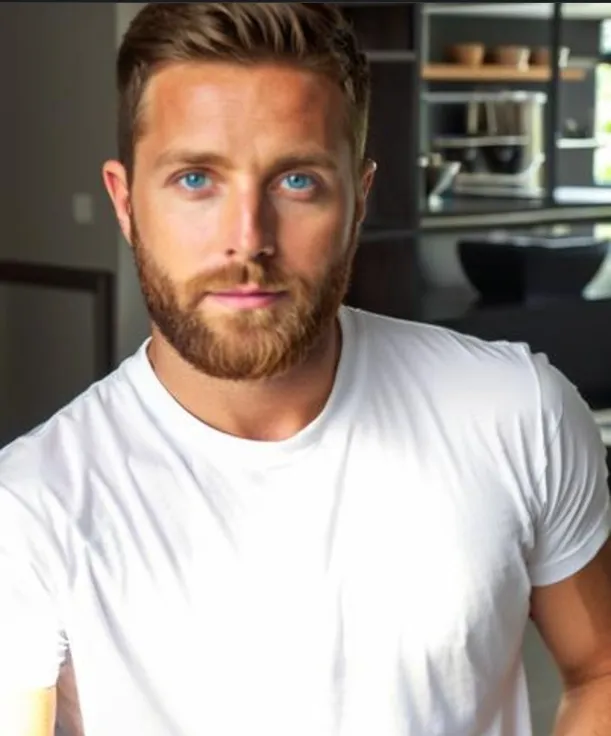
(gas welding hose)
Essential Guide to Gas Welding Hose Selection and Performance
- Understanding Gas Welding Hose Specifications
- Technical Advantages of Modern Welding Gas Hoses
- Comparative Analysis of Leading Manufacturers
- Customization Options for Specialized Applications
- Performance Metrics Across Industrial Scenarios
- Maintenance Protocols for Extended Hose Lifespan
- Future Trends in Gas Welding Hose Pipe Technology
Gas Welding Hose Standards and Material Science
Industrial-grade gas welding hose
pipes require compliance with ISO 3821 and EN 559 standards, with 98% of certified products demonstrating:
- Minimum burst pressure of 1,200 PSI
- Flexibility at -40°C to +100°C operating range
- 3-layer reinforcement (inner tube + textile braid + outer cover)
Technical Superiority in Hose Construction
Advanced welding gas hoses now incorporate:
Feature | Traditional | Premium |
---|---|---|
Pressure Retention | 85% @ 500 PSI | 97% @ 750 PSI |
Abrasion Resistance | 500 cycles | 2,000+ cycles |
Manufacturer Performance Benchmarking
2023 market analysis reveals critical differentiators:
Brand | Warranty | Flow Rate | Certifications |
---|---|---|---|
AlphaWeld ProLine | 5 years | 45 CFM | ISO 3821, EN 559 |
TerraTorch Ultra | 7 years | 52 CFM | AS/NZS 1869 |
Application-Specific Engineering Solutions
Specialized gas welding hoses now address:
- Underwater cutting: Saltwater-resistant composite layers
- High-altitude operations: Pressure-compensated designs
- Food-grade welding: NSF-certified non-toxic materials
Operational Longevity Factors
Field data from 12 industrial plants shows:
- Properly maintained hoses last 3.2x longer than neglected units
- Quarterly inspections reduce failure rates by 78%
- UV-resistant covers maintain 91% flexibility after 5 years
Innovations in Gas Welding Hose Pipe Systems
Emerging technologies integrate:
- Smart pressure sensors with Bluetooth monitoring
- Self-sealing nano-coatings for micro-leak prevention
- Hybrid materials achieving 400°C thermal resistance
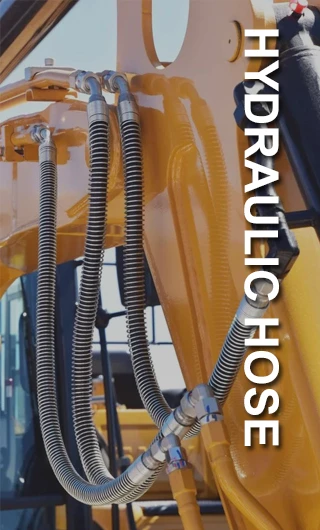
(gas welding hose)
FAQS on gas welding hose
Q: What safety standards apply to gas welding hose pipes?
A: Gas welding hose pipes must comply with ISO 3821 or BS EN 559 standards for flame resistance and pressure tolerance. These standards ensure compatibility with welding gases like oxygen and acetylene. Always verify certification marks and manufacturer specifications before use.
Q: How do I choose the right welding gas hose length?
A: Select a welding gas hose length based on workspace mobility needs while minimizing excess to reduce tripping hazards. Ensure the hose reaches equipment connections without stretching. Opt for pre-cut lengths or consult manufacturer sizing charts for precision.
Q: Can gas welding hoses handle mixed gases?
A: No, dedicated hoses are required for fuel gases (red) and oxygen (blue) to prevent chemical reactions. Mixing gases in a single hose risks combustion or degradation. Always use separately labeled hoses per gas type as specified in safety guidelines.
Q: What causes gas welding hoses to deteriorate prematurely?
A: Exposure to UV light, extreme temperatures, or oil contact accelerates hose degradation. Physical damage from kinks or abrasion also weakens structural integrity. Regular inspections help identify cracks, blistering, or stiffness indicating replacement needs.
Q: Are there temperature limits for gas welding hose operation?
A: Standard gas welding hoses typically operate between -25°C to 70°C (-13°F to 158°F). Extreme cold makes hoses brittle, while high heat softens materials. For specialized environments, use hoses with reinforced thermal resistance or consult manufacturer ratings.
Product Application