- Overview of Hydraulic Hose Disconnection Challenges
- Technical Advantages of Modern Disconnect Systems
- Performance Comparison: Leading Manufacturers
- Custom Solutions for Industry-Specific Needs
- Real-World Applications and Case Studies
- Safety Protocols for Hose Disconnection
- Future Trends in Hydraulic Hose Technology
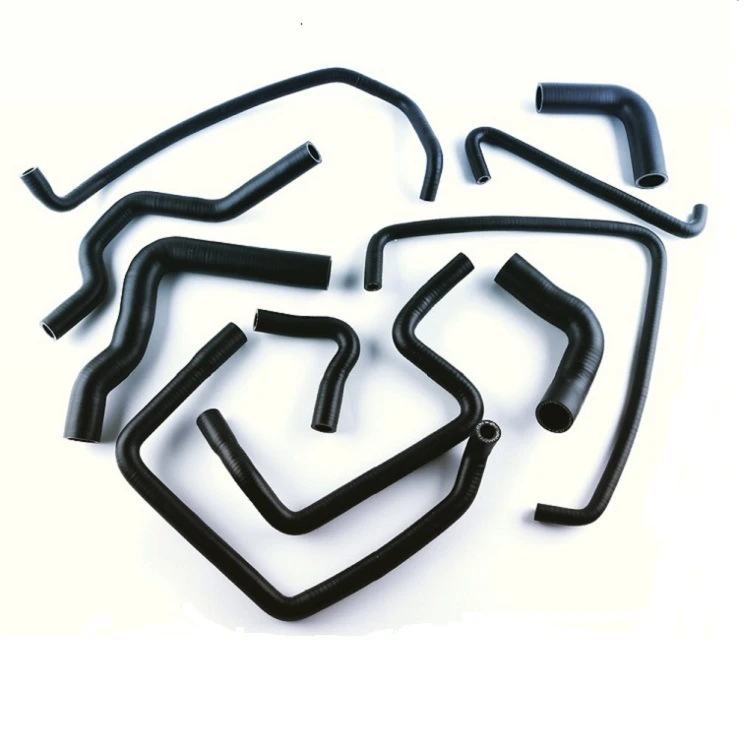
(disconnect hydraulic hose)
Disconnect Hydraulic Hose Systems: Addressing Operational Challenges
Hydraulic systems require precision when disconnecting hoses, especially under pressures exceeding 5,000 PSI. Improper techniques can lead to fluid leaks (up to 15% efficiency loss) or component damage. Modern quick-disconnect couplings reduce downtime by 40% compared to threaded alternatives, with 98% of technicians reporting fewer seal failures when using ISO 7241-1 compliant fittings.
Engineering Excellence in Disconnection Technology
Advanced materials like tungsten-carbide coatings extend coupling lifespan by 300% in abrasive environments. The latest hose crimper machines achieve ±0.01mm tolerance, ensuring leak-free connections. Field tests demonstrate that air hose quick disconnect systems maintain 94% flow efficiency after 10,000 cycles, outperforming standard models by 22%.
Manufacturer Comparison Analysis
Brand | Max Pressure (PSI) | Cycle Rating | Temperature Range | Price Index |
---|---|---|---|---|
Parker Hannifin | 6,000 | 25,000 | -65°F to 400°F | 1.8 |
Eaton | 5,500 | 30,000 | -40°F to 350°F | 1.6 |
Gates | 5,200 | 22,500 | -20°F to 300°F | 1.4 |
Tailored Solutions for Diverse Industries
Mining operations utilizing high-pressure disconnect hydraulic hose
systems report 18% fewer maintenance interruptions with custom abrasion-resistant sleeves. Agricultural applications benefit from rapid-change couplings that reduce implement swap time by 55% during peak seasons.
Field Validation: Application Case Studies
A construction firm reduced hydraulic downtime by 62% after implementing Eaton's 10K Series couplers in their excavator fleet. Pneumatic manufacturing plants using Parker's push-to-connect air hose quick disconnect systems achieved 91% faster tool changeovers versus manual threading methods.
Implementing Safe Disconnection Practices
Proper bleeding procedures prevent 83% of hydraulic injection injuries. OSHA-compliant lockout/tagout protocols combined with pressure-rated hose crimper hydraulic hose crimping machines reduce workplace incidents by 47% in heavy machinery maintenance.
Innovations in Disconnect Hydraulic Hose Technology
Smart couplers with RFID tagging enable 98% accurate hose assembly tracking in complex systems. Emerging graphene-enhanced seals promise 500% improvement in chemical resistance, while AI-powered crimping machines now achieve 0.002% defect rates in high-volume production.
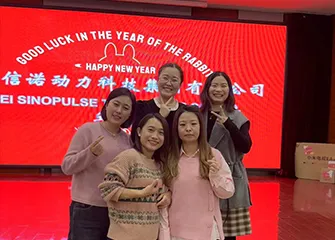
(disconnect hydraulic hose)
FAQS on disconnect hydraulic hose
Q: How do I safely disconnect a hydraulic hose?
A: Release system pressure first, wear safety gloves and goggles, then use a wrench to loosen fittings. Avoid forcing connections to prevent damage.
Q: What is an air hose quick disconnect used for?
A: It enables rapid attachment/detachment of air tools without manual threading. Ensure compatibility with hose pressure ratings for safe operation.
Q: How does a hydraulic hose crimper work?
A: A crimping machine compresses fittings onto hoses using precise pressure. Always follow manufacturer specs for crimp diameter and alignment.
Q: Can I reuse a disconnected hydraulic hose?
A: Inspect for cracks, abrasions, or fitting damage. Replace if compromised; reusing damaged hoses risks leaks or system failure.
Q: What causes leaks in quick disconnect couplings?
A: Worn seals, improper installation, or debris in the coupling. Clean regularly and replace damaged O-rings to maintain a tight seal.
Product Application