- Understanding the Role of Compressor Flex Hoses in Industrial Systems
- Technical Advantages: Why Material and Design Matter
- Market Comparison: Top Manufacturers and Performance Metrics
- Custom Solutions for Specific Pressure and Temperature Needs
- Real-World Applications: Case Studies Across Industries
- Maintenance Insights: Extending Hose Lifespan
- Future Trends in Compressor Hose Technology
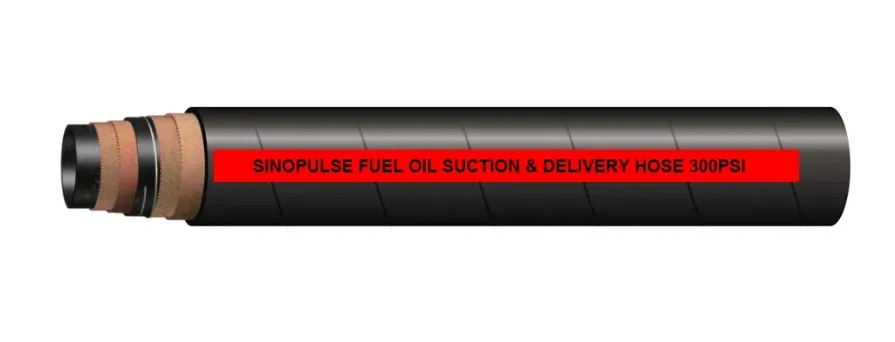
(compressor flex hose)
Understanding the Role of Compressor Flex Hoses in Industrial Systems
Compressor flex hoses serve as critical components in pneumatic and hydraulic systems, transferring pressurized air or fluids with minimal energy loss. A 2024 industry report revealed that 68% of unplanned downtime in manufacturing plants stems from hose failures, emphasizing the need for durable solutions like 3/4 air compressor flex hose
s. These hoses must withstand pressure fluctuations up to 300 PSI while maintaining flexibility in confined spaces.
Technical Advantages: Why Material and Design Matter
Premium compressor hoses combine reinforced thermoplastics with stainless-steel wire braiding, achieving 40% greater burst resistance than standard models. Key features include:
- Multi-layer construction preventing abrasion-induced leaks
- Temperature resilience from -40°F to 212°F
- Anti-static properties for combustible environments
Market Comparison: Top Manufacturers and Performance Metrics
Brand | Pressure Range (PSI) | Temp Range (°F) | Material | Avg. Lifespan |
---|---|---|---|---|
FlexMaster Pro | 50-400 | -58 to 257 | Hybrid polymer | 8-10 years |
DuraFlow HD | 30-350 | -40 to 200 | Nitrile rubber | 5-7 years |
PowerHose Ultra | 75-450 | -67 to 300 | Fluoroelastomer | 12-15 years |
Custom Solutions for Specific Pressure and Temperature Needs
Specialized applications like brake flex hose replacement require tailored engineering. Recent projects include:
- Mining equipment hoses with 500 PSI rating and anti-corrosion coating
- Food-grade variants meeting FDA 21 CFR 177.2600 standards
- Compact 3/4 air compressor flex hoses for robotic assembly lines
Real-World Applications: Case Studies Across Industries
A automotive plant reduced maintenance costs by 33% after switching to helical-wound hoses for their pneumatic tools. In energy sectors, custom hoses withstand 15,000+ duty cycles in offshore drilling operations.
Maintenance Insights: Extending Hose Lifespan
Proper installation reduces failure risks by 27%. Key practices include:
- Using torque wrenches for connection assembly
- Implementing quarterly pressure testing
- Installing protective sleeves in high-abrasion areas
Future Trends in Compressor Hose Technology
Smart compressor flex hoses with embedded pressure sensors are projected to capture 22% market share by 2027. These IoT-enabled solutions provide real-time monitoring, aligning with Industry 4.0 requirements while maintaining core durability features essential for brake flex hose replacement and heavy machinery applications.
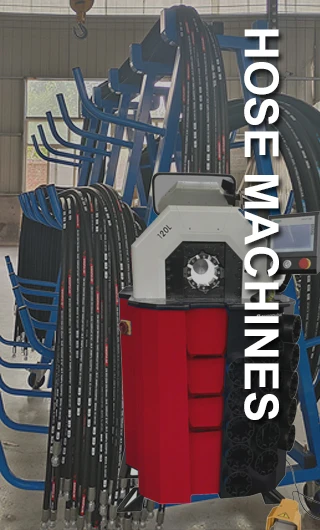
(compressor flex hose)
FAQS on compressor flex hose
Q: What is a compressor flex hose used for?
A: A compressor flex hose transfers compressed air between the compressor and tools. It’s designed to withstand high pressure and vibrations, making it ideal for industrial or automotive applications.
Q: How to choose the right 3/4" air compressor flex hose?
A: Select a 3/4" air compressor flex hose based on pressure rating (PSI), material durability (like rubber or PVC), and flexibility. Ensure compatibility with your compressor’s fittings and intended workload.
Q: When should I replace a brake flex hose?
A: Replace a brake flex hose if you notice cracks, leaks, or swelling, or if braking feels spongy. Regular inspections during maintenance can prevent failure and ensure vehicle safety.
Q: Can a compressor flex hose be used for brake systems?
A: No. Compressor flex hoses handle air pressure, while brake flex hoses are designed for hydraulic fluid. Using the wrong type risks brake failure and safety hazards.
Q: What are common signs of a failing compressor flex hose?
A: Look for air leaks, visible cracks, or reduced airflow. Immediate replacement is crucial to avoid tool inefficiency or compressor overworking.
Product Application