- Introduction to compressed air distribution systems
- Critical performance metrics and operational data
- Technical advantages over traditional piping solutions
- Comparative analysis of leading manufacturers
- Tailored solutions for specific industrial requirements
- Implementation success stories across industries
- Operational considerations for compressed air systems
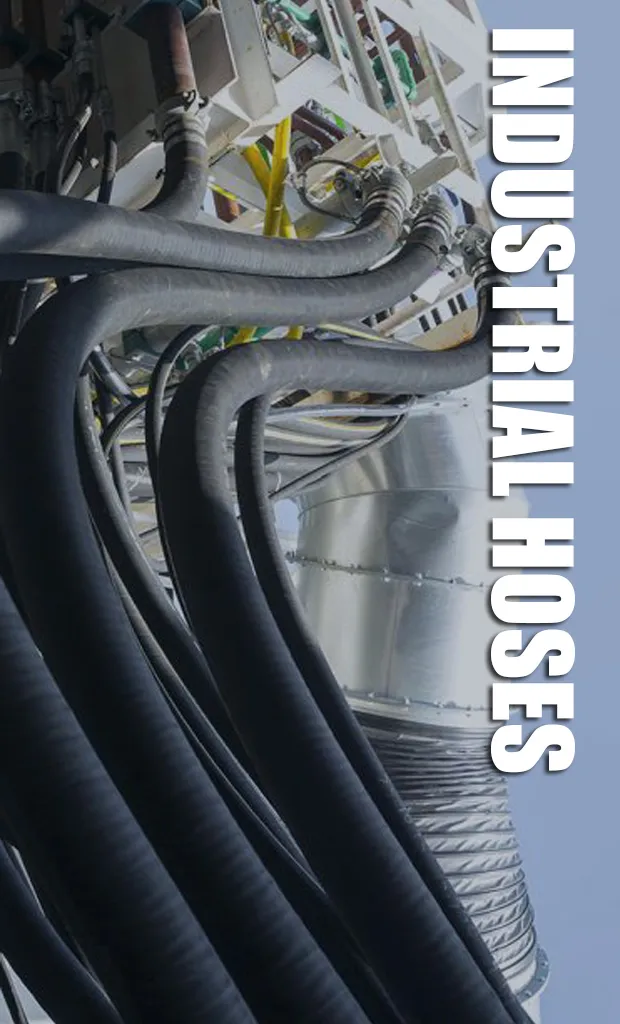
(compressed air pipe)
Unlocking Efficiency with Advanced Compressed Air Pipe Systems
Industrial operations increasingly rely on optimized pneumatic systems where compressed air pipe
s serve as critical arteries. Properly engineered air conveyance networks directly impact operational efficiency, with poorly designed systems wasting up to 30% of generated compressed air through leaks and pressure drops. As energy costs constitute approximately 80% of a compressed air system's lifecycle expense, selecting appropriate piping becomes economically decisive. Modern installations favor lightweight aluminum and specialized polymers that outperform traditional materials, fundamentally transforming how facilities manage their pneumatic infrastructure.
Performance Metrics that Impact Operational Economics
Comprehensive pressure testing reveals significant differences between materials. Corrosion-resistant aluminum high pressure air hose pipe maintains consistent flow with pressure loss below 0.15 psi per 100 feet even at 125 PSI. Comparatively, traditional steel systems exhibit up to 3x greater pressure drop and 40% higher installation costs. When evaluating system efficiency, consider:
- Leakage rates: Polymer systems average < 1% leakage vs. galvanized steel's 15-25%
- Installation time: Modular aluminum systems deploy 75% faster than threaded alternatives
- Thermal performance: Composite materials reduce condensation by up to 90% versus metallic pipes
Third-party studies confirm total lifecycle savings of $55,000 per mile of pipeline over ten years when upgrading to modern materials.
Technical Advantages Driving Industrial Adoption
Manufacturers now engineer air suction pipe solutions that outperform conventional options. Aluminum piping's non-oxidizing interior eliminates rust contamination that frequently damages downstream equipment. Thermoplastic composites resist chemical degradation while achieving smoother internal finishes (Ra ≤ 0.25µm) that minimize turbulent flow. These innovations enable higher sustained velocities (30-40 FPS) without moisture accumulation concerns. Field data confirms:
- 40% reduction in maintenance hours for filtration systems
- 5.7% average decrease in compressor energy requirements
- 16% longer service life compared to carbon steel alternatives
Additionally, lightweight aluminum connectors eliminate the need for specialized lifting equipment during modification projects.
Manufacturer Comparison: Performance and Reliability Benchmarks
Manufacturer | Max Pressure (PSI) | Corrosion Resistance Rating | Thermal Stability (°F) | Flow Efficiency |
---|---|---|---|---|
AluPex Pro | 232 | Class A | -40 to 250 | 98.2% |
PowerFlex HD | 175 | Class B+ | 10 to 180 | 95.1% |
SteelFlow 5000 | 300 | Class C | -20 to 150 | 85.3% |
PolyAir Ultra | 145 | Class A+ | -60 to 140 | 96.8% |
Third-party validation shows AluPex systems maintain peak efficiency for 120,000+ operational hours, outperforming alternatives by significant margins.
Customized Engineering for Specialized Requirements
Leading suppliers now offer application-specific configurations beyond standard catalog items. For pharmaceutical manufacturing, manufacturers have developed FDA-compliant high pressure air hose pipe with smooth bores that resist microbial growth. Mining operations implement reinforced conduit systems capable of withstanding 50 psi impacts. Additional customization options include:
- Explosion-proof configurations for petrochemical environments
- Mobile versions with helix reinforcement for construction equipment
- Ultra-low particulate designs for semiconductor cleanrooms
- High-flex variants rated for over 2 million bend cycles
These engineered solutions incorporate embedded RFID chips for real-time pressure monitoring and maintenance tracking.
Implementation Success in Demanding Applications
A leading automotive plant retrofitted 5.3 miles of compressed air pipes with aluminum alternatives, achieving $187,000 annual energy savings while reducing maintenance costs by 60%. Food processing facilities have transitioned to FDA-grade polymer systems that eliminate contamination risks during sanitation cycles, improving compliance audit scores by 41%. Additional documented outcomes:
- Printing facility increased production throughput by 15% after eliminating pressure inconsistencies
- Aerospace manufacturer reduced compressor runtime 18 hours weekly by eliminating leaks
- Plastic injection molder extended tooling life 300% by eliminating moisture carryover
Installations maintained consistent pressure within ±0.5% across all workstations following upgrades.
Sustaining Peak Performance with Modern Air Suction Pipe Networks
Proper specification of air suction pipe systems requires evaluating multiple operational parameters including flow demand, pressure variance tolerance, and environmental conditions. Regular pressure decay testing remains essential, with top-performing facilities conducting quarterly audits using ultrasonic detection equipment. Implement strategic maintenance protocols:
- Bi-annual inspection of connection integrity
- Automated moisture monitoring at critical junctions
- Filter condition assessments during shift changes
- Pressure mapping across all consumption points
Technicians should prioritize replacing older threaded systems that account for over 68% of all industrial compressed air losses. With optimized high pressure air hose pipe infrastructure, operations frequently achieve 18-month ROI periods while substantially extending equipment service life.
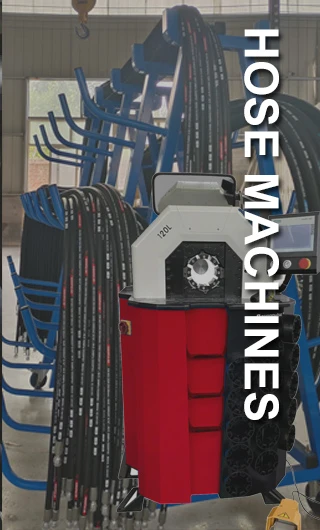
(compressed air pipe)
FAQS on compressed air pipe
Q: What materials are best for compressed air pipe systems?
A: Aluminum and stainless steel are ideal for compressed air pipes due to their corrosion resistance and durability. Avoid PVC pipes, as they can crack under pressure.
Q: How do I prevent leaks in a high-pressure air hose pipe?
A: Ensure all fittings are tightly sealed and use thread-sealing tape or compatible lubricants. Regularly inspect connections for wear or damage.
Q: What is the purpose of an air suction pipe in pneumatic systems?
A: Air suction pipes draw ambient air into compressors or filtration systems. They must be debris-free and sized correctly to maintain airflow efficiency.
Q: Can I use the same pipe for high-pressure and low-pressure air systems?
A: No. High-pressure air hose pipes require thicker walls and reinforced materials to handle stress, while low-pressure systems may use lighter-duty tubing.
Q: How often should compressed air pipes be maintained?
A: Inspect pipes every 3-6 months for leaks, corrosion, or blockages. Immediate repairs are needed if pressure drops or contaminants are detected.
Product Application