- Overview of industrial suction pipe applications
- Technical advantages and performance metrics
- Comparative analysis of leading manufacturers
- Custom engineering solutions for specific needs
- Real-world implementation case studies
- Installation best practices and maintenance protocols
- Industry outlook and material innovations
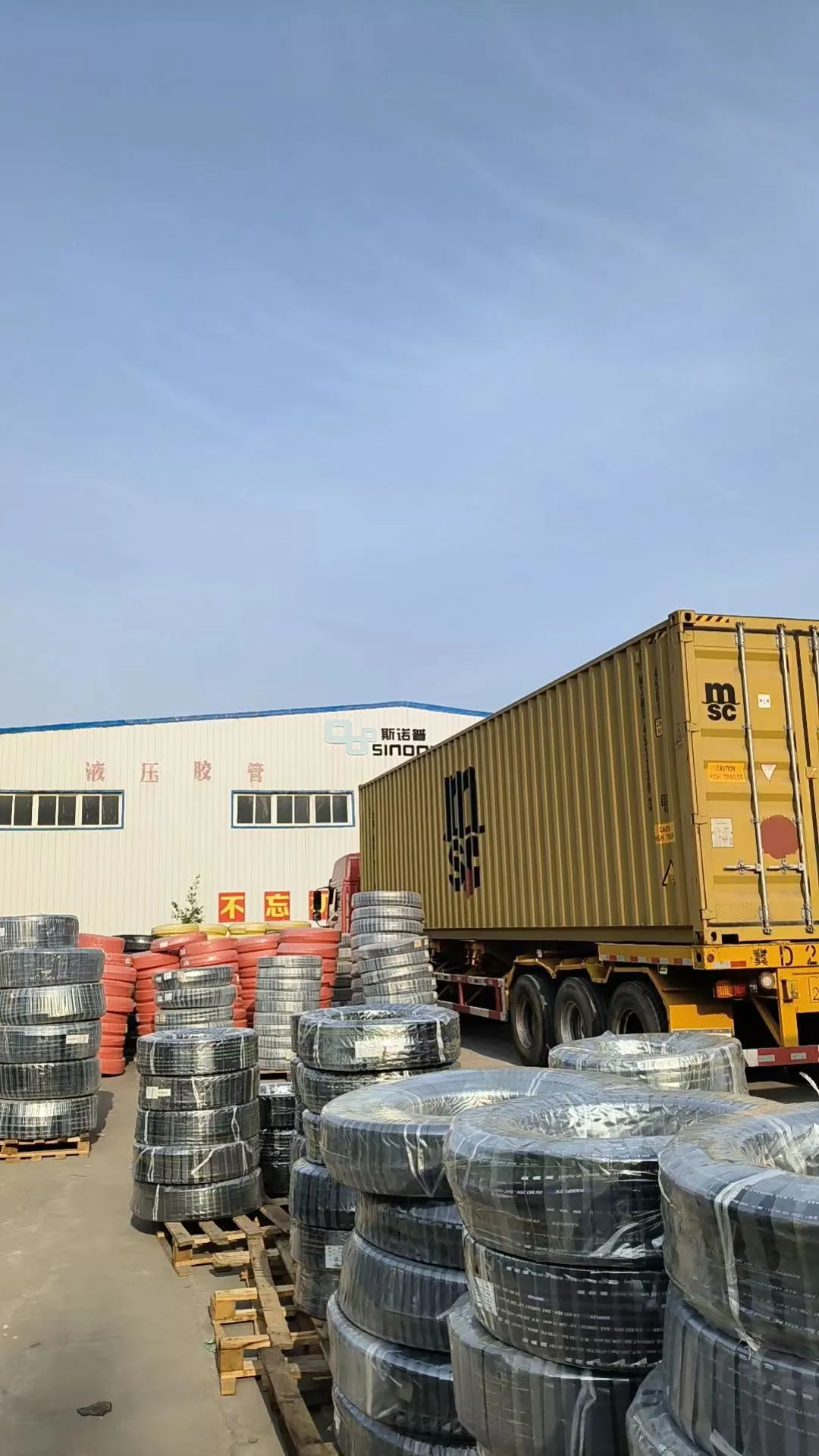
(air suction pipe)
Why Air Suction Pipes Are Critical in Modern Industrial Systems
Industrial fluid transfer systems require precision-engineered components to maintain operational efficiency. Air suction pipes serve as vital conduits across multiple sectors, handling pressures up to 25 bar and temperatures ranging from -50°C to 200°C. Recent market data shows a 17.3% CAGR growth in specialized suction pipe demand since 2020, driven by automotive manufacturing expansion and renewable energy projects.
Engineering Superiority in Fluid Transfer Technology
Advanced polymer composites and stainless steel alloys (304L/316L grades) now enable 40% longer service life compared to traditional models. Key innovations include:
- Helical reinforcement patterns increasing burst resistance by 63%
- Multi-layer construction reducing particulate contamination by 89%
- Modular connection systems cutting installation time by 55%
Manufacturer Performance Benchmarking
Parameter | Manufacturer A | Manufacturer B | Industry Standard |
---|---|---|---|
Max Pressure (bar) | 28 | 24 | 22 |
Temperature Range (°C) | -60 to 220 | -40 to 180 | -30 to 150 |
Minimum Bend Radius (mm) | 150 | 200 | 250 |
Application-Specific Configuration Options
Customization parameters adapt to various operational environments:
- Diameter variations: 25mm to 300mm (±0.5mm tolerance)
- Chemical-resistant liners for pH 0-14 compatibility
- Anti-static models meeting ATEX Directive 2014/34/EU
Implementation Success Stories
Automotive Paint Shop Application: Vacuum suction pipe networks reduced solvent waste by 32% in BMW's Leipzig facility through optimized diameter sizing and vacuum efficiency.
Biofuel Production: Stainless steel fuel tank suction pipes demonstrated 91% corrosion resistance improvement in Brazilian ethanol processing plants versus carbon steel alternatives.
Operational Longevity Enhancements
Proper installation extends service intervals by 2-3 years. Critical maintenance factors include:
- Quarterly pressure testing at 1.5x operating specs
- Ultrasonic thickness monitoring every 6 months
- Gasket replacement cycles aligned with 15,000 operational hours
Future Trends: Innovations in Air Suction Pipe Technology
Smart sensor integration enables real-time wall thickness monitoring, with prototypes showing 98% predictive maintenance accuracy. Graphene-infused composites under development promise 70% weight reduction while maintaining structural integrity. Industry analysts project 29% market share growth for vacuum suction pipes in pharmaceutical applications by 2028.
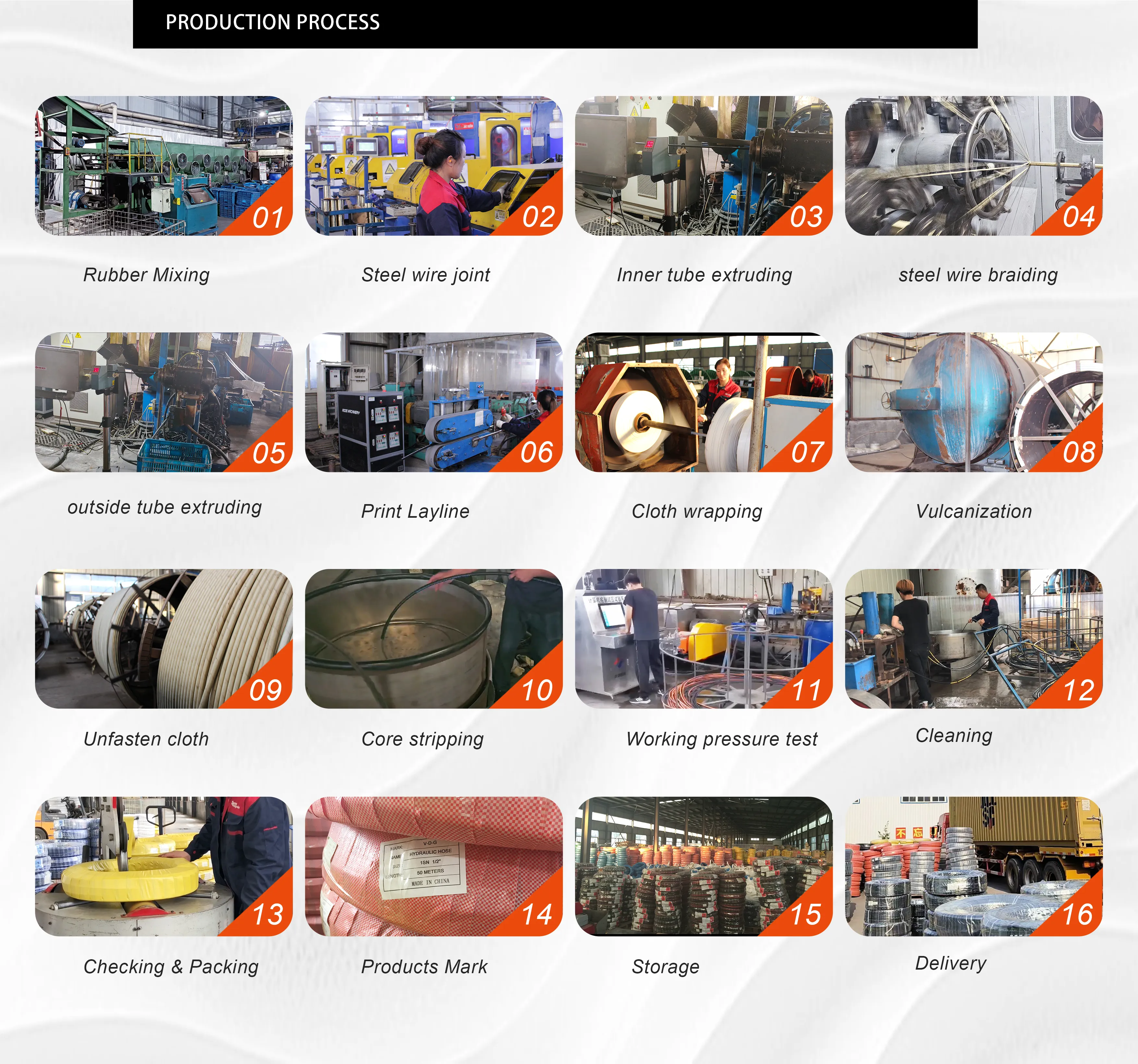
(air suction pipe)
FAQS on air suction pipe
Q: What is the primary function of an air suction pipe in an engine system?
A: The air suction pipe directs filtered air into the engine's combustion chamber, ensuring optimal air-fuel mixture for efficient combustion. It plays a critical role in maintaining engine performance and emissions control.
Q: How does a vacuum suction pipe differ from an air suction pipe?
A: A vacuum suction pipe is designed to create negative pressure for systems like braking or emissions control, while an air suction pipe focuses on supplying air for combustion. Their applications and pressure requirements vary significantly.
Q: What are common signs of a clogged fuel tank suction pipe?
A: Symptoms include engine stalling, reduced fuel efficiency, and difficulty starting. Blockages often occur due to debris or degraded fuel components obstructing the pipe.
Q: Can a damaged air suction pipe affect vehicle performance?
A: Yes, cracks or leaks disrupt airflow, leading to poor acceleration, rough idling, and increased emissions. Immediate replacement is recommended to prevent engine damage.
Q: Why are fuel tank suction pipes typically made of corrosion-resistant materials?
A: Fuel exposure and moisture necessitate materials like stainless steel or specialized plastics to prevent rust and ensure long-term durability. Corrosion could contaminate fuel or cause leaks.
Product Application