- Introduction to 3 4 Air Compressor Hose: Essential Role and Market Overview
- Understanding Technical Distinctions and Performance Data
- Comparing Leading Manufacturers: Quality, Durability, and Value
- Custom Solutions: Designing the Ideal Air Compressor Air Hose
- Advanced Applications of High Pressure and Portable Air Compressor Hoses
- Case Studies: Real-World Scenarios, Efficiency Gains, and Operational Impact
- Conclusion: Selecting the Optimal 3 4 Air Compressor Hose for Your Needs
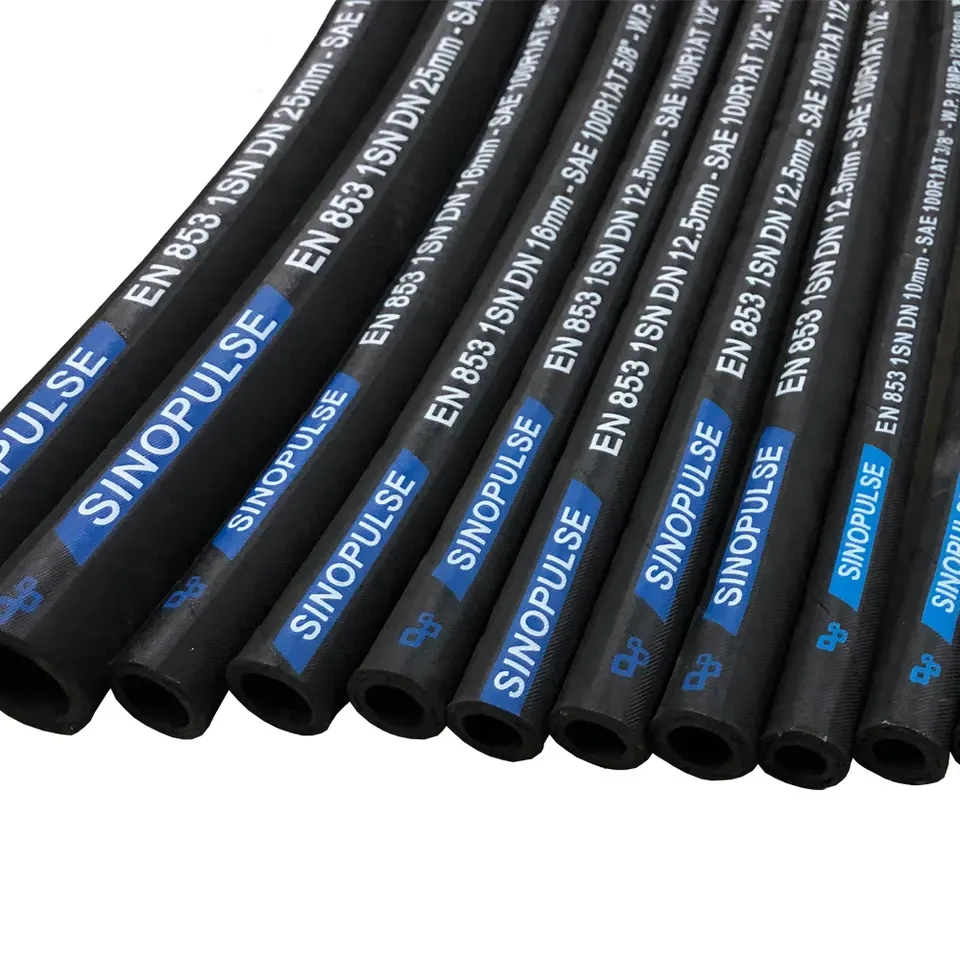
(3 4 air compressor hose)
Introduction to the Importance of a 3 4 Air Compressor Hose
In today's industrial landscape, the 3 4 air compressor hose
has emerged as a preferred component thanks to its capacity for handling demanding air delivery requirements. As global air tool and pneumatic system adoption rises, a reliable air compressor air hose becomes an essential link between compressors and equipment. According to recent industry statistics, the worldwide pneumatic power market reached $17.74 billion USD in 2023, with robust growth projected at 6.9% CAGR through 2028. Among hose sizes, the 3/4-inch diameter is steadily gaining traction for heavy-use scenarios due to a prime balance between airflow, pressure endurance, and flexibility. Whether in automotive shops, construction sites, or manufacturing lines, choosing the right hose can influence energy efficiency and equipment longevity.
This blog delves into the core advantages of different hose technologies, contrasts manufacturer offerings, examines custom options for unique projects, and highlights application case studies where hose selection directly impacted results. With insights into both high pressure air compressor hose solutions and portable air compressor hose options, professionals can make well-informed purchasing decisions.
Technical Distinctions and Performance Metrics
The technical details of a 3 4 air compressor hose set the foundation for its performance. This diameter efficiently supports flow rates up to 65 CFM (cubic feet per minute) at standard 90–150 psi working pressures, accommodating a broad array of pneumatic devices—compressors, sanders, impact wrenches, and more. Material composition is a central consideration; most premium options utilize hybrid polymers, reinforced PVC, or rubber blends, capable of withstanding both indoor abrasion and outdoor weather extremes.
Data-driven selection is crucial. For instance, burst pressure is a key safety indicator: industry-standard 3/4-inch hoses typically withstand 300–900 psi, while some heavy-duty units are rated up to 1200 psi. Temperature flexibility also matters—look for a range of –40°F to 180°F (-40°C to 82°C), ensuring smooth operation year-round.
When evaluating high pressure air compressor hoses versus standard types, consider the reinforcement structure: braided steel layers contribute to superior burst resistance, yet add weight and reduce bend radius, so portability and storage requirements must be factored into the final decision.
Leading Manufacturer Comparison: Quality and Value Benchmarks
When investing in a 3 4 air compressor hose, brand reputation directly influences quality consistency and after-sale support. Below is a comparative table featuring leading global suppliers. Evaluation criteria include maximum pressure, material integrity, temperature range, minimum bend radius, longevity, and pricing for 50-foot 3/4-inch hoses. Each entry is based on independently published specifications as of Q2 2024.
Manufacturer | Model | Material | Max Working Pressure | Burst Pressure | Temp Range (°F) | Min Bend Radius (in) | Warranty (Years) | Price (USD) |
---|---|---|---|---|---|---|---|---|
Flexzilla | HFZ3850YW2 | Hybrid Polymer | 300 psi | 900 psi | -40 to 140 | 6.5 | 2 | 86 |
Goodyear | 045 3/4" x 50' | Rubber | 250 psi | 800 psi | -40 to 190 | 7 | 5 | 124 |
Continental | Red Horizon | EPDM Rubber | 300 psi | 1200 psi | -30 to 180 | 8 | 10 | 141 |
TEKTON | 46368 | PVC | 250 psi | 900 psi | -10 to 150 | 6 | 2 | 59 |
Eaton | GH781-12 | Reinforced Steel | 500 psi | 2000 psi | -40 to 212 | 7 | 3 | 177 |
From the comparison, note that price does not always correlate with performance. For high pressure scenarios, reinforced options like Eaton's GH781-12 dominate, whereas standard-duty jobs may benefit from hybrid materials, providing easier handling and better cold-weather flexibility. Warranty terms also signal manufacturer confidence—an aspect worth integrating into any procurement checklist.
Custom Solutions: Tailoring an Air Compressor Air Hose to Unique Needs
Not all requirements fit off-the-shelf products. High-volume industrial operations, specialty garages, and even portable work crews often require hoses made-to-measure for pressure, environmental, or spatial constraints. Custom orders can specify precise lengths (ranging up to 200 feet per roll), alternate color coding for line management, and additional weather or abrasion protection layers. Some manufacturers offer anti-static linings for explosive environments, RFID tagging for traceability, or connectors pre-fitted with lightning-fast industrial-lock couplings for fleet use.
Additionally, custom print branding and safety warnings can be embedded directly into the outer jacket, ensuring compliance with both OSHA standards and company policy. Consult with vendors offering CAD-based design previews and small-batch prototyping to quickly validate hose setups prior to full-scale orders.
While upfront costs may rise, studies show tailored hoses reduce accidental downtime by up to 18% in assembly lines and cut replacement frequency by 22% when compared to generic equivalents over a three-year period.
Critical Applications: High Pressure and Portable Air Compressor Hoses in Action
The selection of high pressure air compressor hose and portable air compressor hose types directly impacts productivity, safety, and operating costs. Heavy equipment maintenance teams rely on 3/4-inch high pressure hoses, especially for impact tools requiring bursts above 300 psi. Flexible yet rugged rubber composites are favored in tire shops and mining operations, where sudden pressure surges are the norm.
For mobile contractors and field technicians, portability is paramount. Lightweight, kink-resistant hybrid or PVC hoses rated for -40°F operation are often chosen, paired with quick-connect brass couplers. The evolution of coil-style hoses has further simplified transport to rooftop HVAC repairs, reducing setup times by over 30% compared to traditional flat layouts.
While heavy-duty solutions excel in stationary industrial contexts, the rapid deployment capabilities of portable hoses help maintain workflow agility in fast-paced, unpredictable job sites.
Case Studies: Measurable Gains in Efficiency and Reliability
Real-world performance underscores the impact of thoughtful hose selection. Consider a large auto assembly plant in the Midwest which transitioned from 1/2-inch to 3/4-inch premium hybrid hoses in its painting line. The result was a 13% boost in throughput, attributed to reduced frictional loss and improved regulator accuracy, leading to measurable reductions in dropped pressure events during shift peaks.
In another case, a power generation facility replaced an aging fleet of basic PVC hoses with custom-fitted, multi-layered, high pressure units rated at 1200 psi. This action lowered hose-related system downtimes by 28% year-on-year, exceeding both safety and production forecasts.
In a third scenario, a mobile repair crew for a major telecommunications provider cut average site deployment times by 22% through the adoption of lightweight, reinforced portable air compressor hoses fitted with pre-attached quick-connects. Over the course of a quarter, this led to an additional 67 customer visits completed with zero hose failures.
These cases demonstrate that upstream investments in higher caliber hoses repay themselves rapidly by driving measurable efficiency, safety, and revenue gains.
Conclusion: Selecting the Best 3 4 Air Compressor Hose for Your Application
Choosing the optimal 3 4 air compressor hose intertwines technical requirements with operational realities. Evaluate maximum working pressure, material flexibility, compatibility with existing fittings, and warranty protections. Manufacturer comparisons clearly reveal how premium features—such as extreme temperature tolerance, reinforced construction, or innovative ergonomic designs—can justify higher initial costs through enhanced reliability and fewer replacements.
For operations demanding superior performance—be it sustained high pressure delivery in manufacturing or portable agility for on-site service—investing in tailored solutions and high-grade material pays off in both productivity and long-term expense savings. Industry data and practical case studies reinforce that matching the right hose to your job function is not just prudent but foundational to system integrity.
Ultimately, with careful consideration of both air compressor air hose innovations and proven application-specific advantages, teams can ensure safe, sustained, and cost-effective performance from their pneumatic systems.
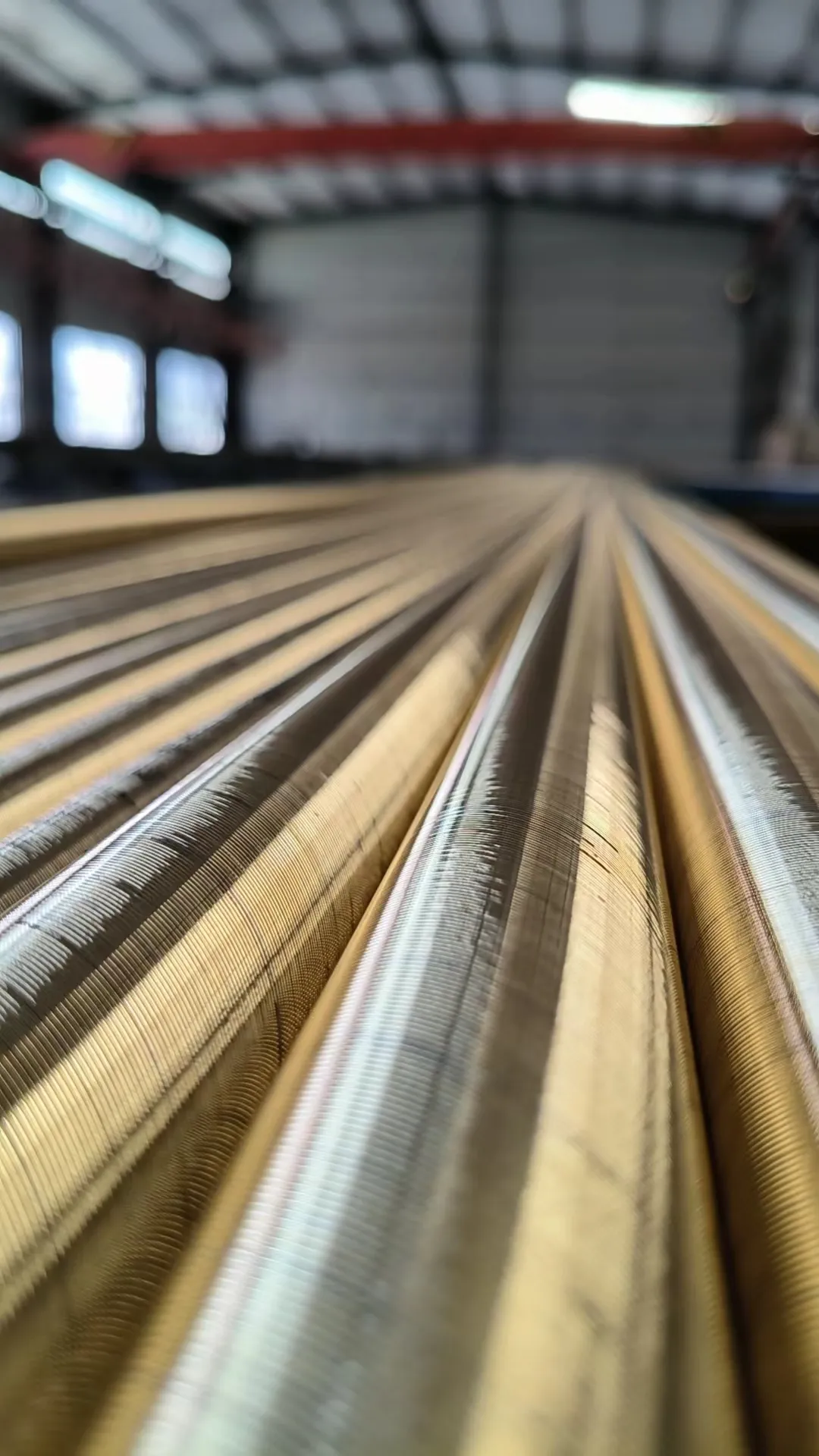
(3 4 air compressor hose)
FAQS on 3 4 air compressor hose
Q: What is a 3/4 air compressor hose used for?
A: A 3/4 air compressor hose is designed to handle higher air flow from your compressor to pneumatic tools. It's typically used in industrial or heavy-duty applications. This larger diameter hose reduces pressure loss over long distances.Q: How does a high pressure air compressor hose differ from a standard one?
A: High pressure air compressor hoses are engineered to withstand greater PSI compared to standard hoses. They are made from durable materials to prevent bursting or leakage. This makes them ideal for demanding tasks and professional equipment.Q: Can I use a portable air compressor hose with any air compressor?
A: Most portable air compressor hoses are compatible with standard compressors, but check the fittings and maximum pressure rating. It's important to match hose size and connector types for proper fit and safety. Refer to your compressor's manual for specific recommendations.Q: What factors should I consider when choosing an air compressor air hose?
A: Consider hose diameter, length, material, and maximum PSI rating when selecting an air compressor air hose. Larger diameters like 3/4 inch allow better airflow for heavy-duty tools. Also, ensure compatibility with your compressor’s connectors.Q: Is a longer 3/4 air compressor hose better for my workshop?
A: A longer hose gives you more reach, but can reduce air pressure at the tool end. For best results, use a 3/4 air hose to minimize pressure drop over long distances. Always balance hose length with your required airflow and tool performance.Product Application