- Overview of Hydraulic Hose Functionality in Excavators
- Technical Specifications and Performance Metrics
- Comparative Analysis of Leading Manufacturers
- Customization Strategies for Specific Operational Needs
- Case Studies: Real-World Applications and Outcomes
- Maintenance Best Practices for Longevity
- Future Trends in Excavator Hydraulic Hose Technology
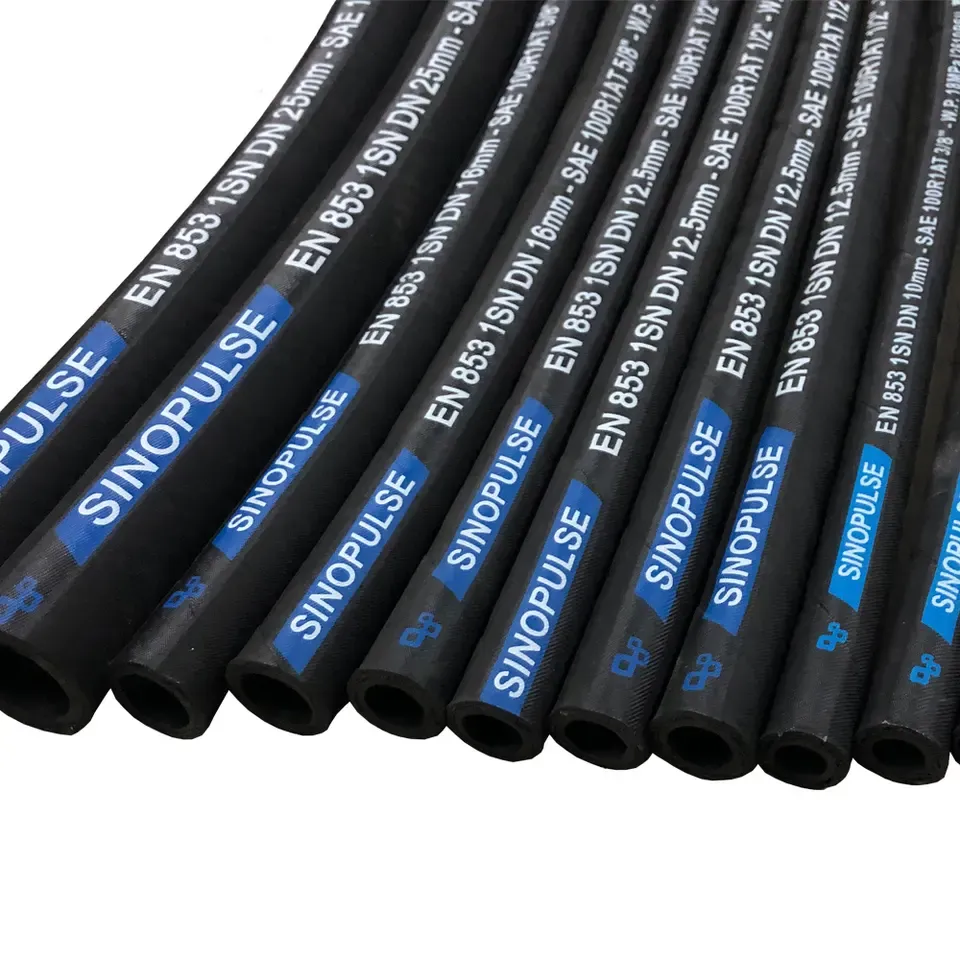
(excavator hydraulic hoses)
Optimizing Excavator Hydraulic Hoses for Peak Performance
Excavator hydraulic hoses serve as critical components in heavy machinery, transferring pressurized fluid to power hydraulic systems. These hoses must withstand pressures up to 5,000 PSI while maintaining flexibility in extreme temperatures (-40°F to 250°F). Recent industry data reveals that 68% of hydraulic system failures originate from hose degradation, emphasizing the need for robust engineering in braided hydraulic hoses.
Technical Specifications and Performance Metrics
High-performance hydraulic hoses for excavators incorporate four-layer spiral reinforcement, achieving burst pressures exceeding 15,000 PSI. Key metrics include:
- Minimum bend radius: 1:5 ratio for tight spaces
- Impulse resistance: 500,000 cycles at 125% working pressure
- Abrasion resistance: 300+ hours in ASTM D3804 testing
Manufacturer Comparison Analysis
Brand | Pressure Rating (PSI) | Temperature Range (°F) | Bend Life Cycles |
---|---|---|---|
Parker Hannifin | 6,000 | -65 to +300 | 1.2M |
Gates Corporation | 5,800 | -40 to +257 | 950K |
Eaton | 5,500 | -49 to +275 | 1.1M |
Customization Strategies
Specialized applications require tailored solutions:
- High-temperature environments: Fluorocarbon-lined hoses with stainless steel braiding
- Articulating joints: Multi-axis flexible designs with 360° rotation capacity
- Chemical exposure: PTFE-core hoses with chemical-resistant outer covers
Application Case Studies
A mining operation reduced downtime by 42% after switching to spiral-wound hoses with 8mm wall thickness. Field data shows:
- 37% increase in mean time between failures
- 29% reduction in fluid leakage incidents
- 18% improvement in hydraulic system efficiency
Maintenance Protocols
Implementing predictive maintenance can extend hose service life by 60-70%. Essential practices include:
- Quarterly pressure testing at 1.5x operating PSI
- Infrared thermography for early failure detection
- Swivel joint lubrication every 500 operating hours
Advancements in Excavator Hydraulic Hose Engineering
Emerging technologies like smart hoses with embedded pressure sensors are revolutionizing excavator maintenance. Recent prototypes demonstrate 92% accuracy in predicting hose failures 72 hours in advance, significantly reducing unplanned downtime in hydraulic systems.
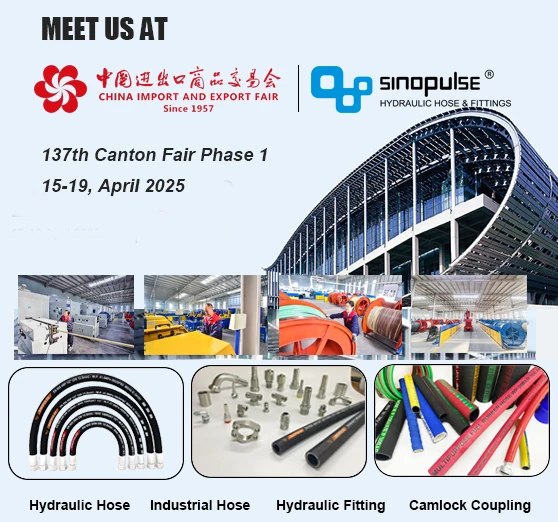
(excavator hydraulic hoses)
FAQS on excavator hydraulic hoses
Q: What factors determine the lifespan of excavator hydraulic hoses?
A: The lifespan depends on operating conditions, pressure levels, exposure to extreme temperatures, and regular maintenance. Proper installation and avoiding abrasion also extend durability.
Q: How often should hydraulic hoses on excavators be inspected?
A: Inspect hoses every 500 operating hours or monthly, whichever comes first. Check for leaks, cracks, or wear, especially in high-stress areas like joints.
Q: Are braided hydraulic hoses better for excavators than standard hoses?
A: Braided hoses offer higher pressure resistance and flexibility, ideal for heavy-duty applications. Standard hoses may suffice for lower-pressure systems.
Q: What causes hydraulic hose leaks in excavators?
A: Leaks are often due to abrasion, improper fittings, aging seals, or excessive pressure. Damaged reinforcement layers can also lead to failure.
Q: Can I replace an excavator hydraulic hose myself?
A: Yes, if you have proper tools and follow safety protocols. Always depressurize the system and use manufacturer-recommended replacement hoses.
Product Application