Hydraulic flex hoses have become indispensable components in modern industrial operations, serving as the vital link between mechanical systems and fluid power transmission. These engineered solutions combine flexibility with strength, allowing for efficient energy transfer while accommodating movement and vibration in dynamic industrial environments. The development of hydraulic flex hoses has progressed significantly from simple rubber tubes to sophisticated multi-layered structures capable of handling extreme pressures, temperatures, and corrosive media. In today's automated manufacturing plants, construction sites, and agricultural operations, the reliability of these hoses directly impacts system performance, operational safety, and maintenance costs. Their ability to maintain integrity under continuous flexing and pressure cycling makes them superior to rigid piping in most mobile and semi-permanent installations.
Hydraulic Flex Hose in Fluid Transfer Systems
Die Rolle von hydraulic flex hoses in fluid transfer systems extends far beyond simple conduit functions. Modern water suction and discharge hoses incorporate specialized designs to handle both vacuum and pressure conditions, with reinforced walls that prevent collapse during high-volume pumping operations. These hoses often feature smooth inner liners that minimize turbulence and pressure drop, significantly improving energy efficiency in large-scale irrigation and dewatering applications.
For petroleum-based applications, advanced oil suction and discharge hoses utilize synthetic rubber compounds resistant to hydrocarbon degradation while maintaining flexibility across wide temperature ranges. When selecting high-pressure hoses, such as 20 bar hoses for industrial applications, engineers must consider not just pressure ratings but also compatibility with specific fluids, temperature extremes, and potential chemical exposure.
The installation of hydraulic flex hoses in fluid systems requires careful attention to routing and support. Proper practices include maintaining recommended bend radii, using protective sleeves in high-abrasion areas, and implementing proper clamping techniques to prevent stress concentrations. These measures ensure optimal performance and extended service life, reducing downtime and maintenance costs in critical industrial operations.
Hydraulic Flex Hose in Abrasion and Chemical Resistance
The demanding environments of mining, construction, and material handling have driven significant innovations in abrasion-resistant hoses. In underground mining applications, these special hoses must be able to withstand not only wear and tear but also chemicals, oil, and extreme temperatures while maintaining flexibility in a narrow workspace.
Fuel oil hoses represent another critical application where material science breakthroughs have yielded impressive results. New fluoropolymer-based constructions provide unprecedented resistance to petroleum products and environmental factors such as ultraviolet rays and ozone. The development of 300 psi Schläuche with enhanced chemical resistance has been particularly valuable in industrial cleaning applications, where equipment must handle aggressive solvents and high-pressure jets simultaneously.
For compressed air systems, 20 bar air hoses now incorporate anti-microbial layers to prevent bacterial growth in moisture-prone environments while maintaining flexibility in cold weather conditions. Sinopulse uses advanced testing methods to verify the performance, including accelerated aging tests, chemical immersion tests, and real-world wear simulations, which far exceed the basic pressure test requirements.
Hydraulic Flex Hose in High-Pressure and Specialized Applications
The evolution of high-pressure hydraulic flex hoses has enabled remarkable advancements in industrial machinery and equipment.
In dredging and material handling operations, heavy-duty abrasion hoses combine wear-resistant exteriors with innovative reinforcement patterns that optimize flexibility while resisting crushing forces. The latest designs feature real-time monitoring capabilities, with embedded sensors that track pressure, temperature, and wear patterns to predict maintenance needs before failures occur.
The connection technology for hydraulic flex hoses has seen parallel advancements, with new crimping techniques and fitting designs that ensure leak-proof performance even under constant vibration and movement. Industry standards are constantly developing, and recent updates have solved new requirements, such as fire resistance, low-temperature flexibility, and compatibility with bio-based hydraulic oils. Now, the appropriate system design includes not only the hoses themselves but also intelligent wiring, appropriate supporting structures, and a comprehensive maintenance agreement to maximize service life in these demanding applications.
With the industries advancing to higher automation and efficiency, hydraulic flex hoses are constantly adapting, and intelligent hose technologies and advanced materials set new benchmarks for performance and reliability. The ongoing development of these critical components remains essential to meeting the ever-increasing demands of modern industrial operations.
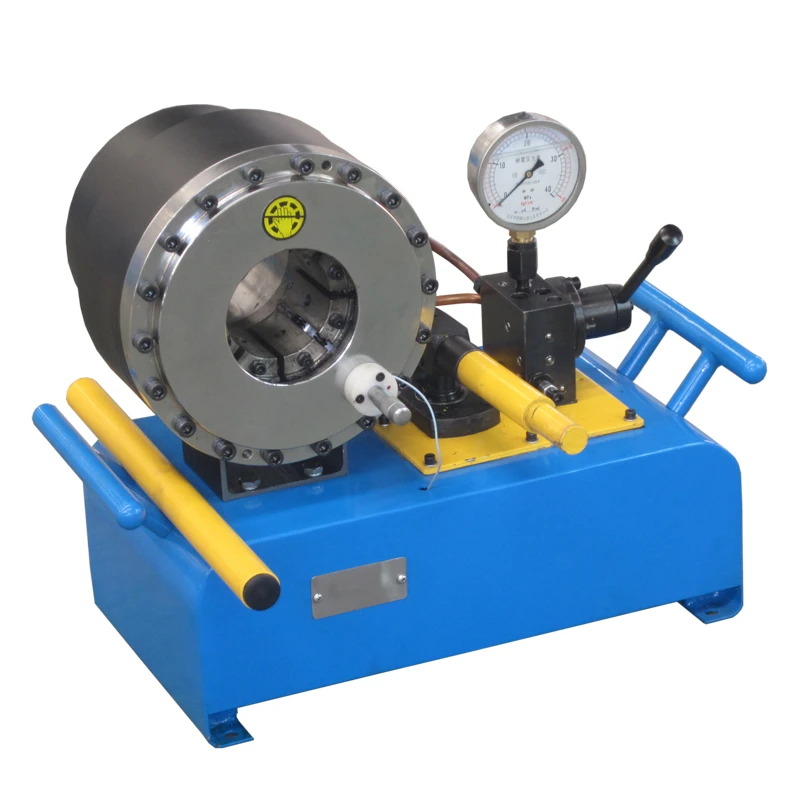
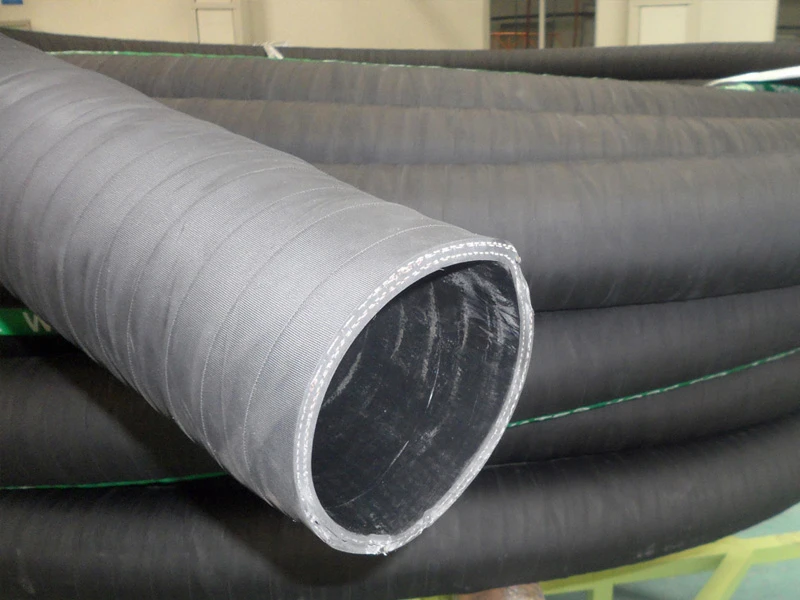
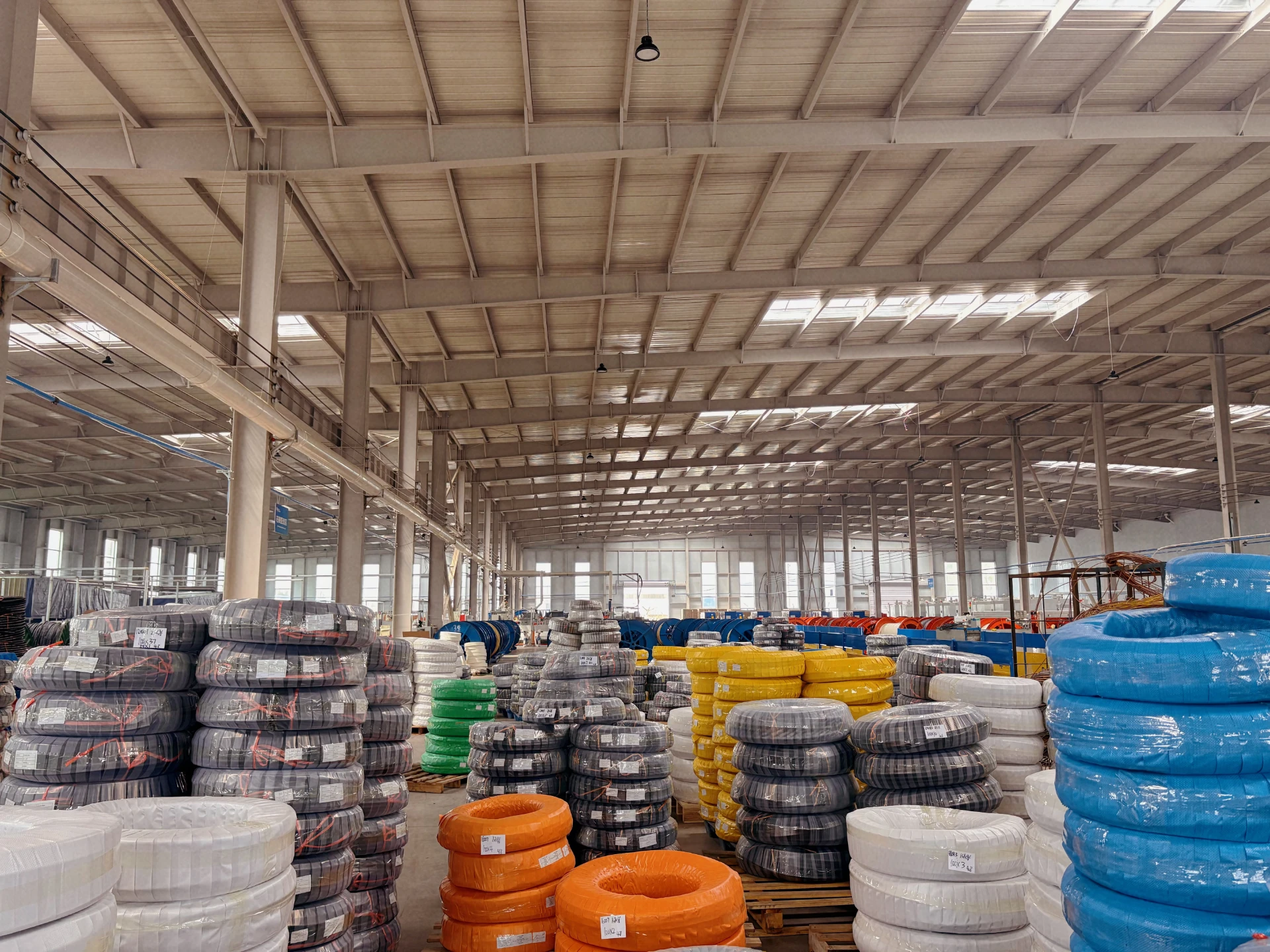
Produktanwendung