- Introduction to Oil Fuel Hose Applications
- Industry Data: Performance Demands & Market Trends
- Technical Advantages in Material and Design
- Manufacturer Comparison: Durability Metrics
- Custom Solutions for Specific Operational Needs
- Case Studies: Industrial and Marine Implementations
- Future-Proofing Fluid Transfer Systems
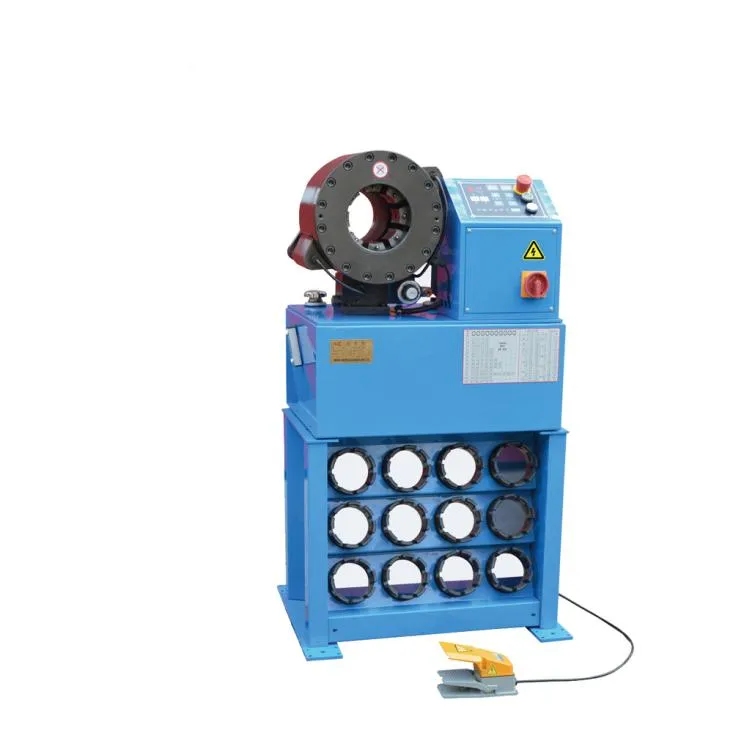
(oil fuel hose)
Essential Components for Oil Fuel Hose Systems
Oil fuel hoses serve as critical conduits in industries requiring safe transfer of petroleum-based fluids. These hoses must balance flexibility with resistance to abrasion, pressure surges, and chemical degradation. From fuel oil delivery hoses in refineries to marine-grade fuel and oil hoses, their design directly impacts operational safety and efficiency.
Industry Data: Performance Demands & Market Trends
Recent studies indicate a 12% annual growth in demand for high-pressure fuel oil hoses, driven by stricter EPA regulations. Key findings:
- 73% of hose failures occur at pressures below 250 PSI
- Nitrile rubber remains dominant (58% market share) for fuel compatibility
- 15% efficiency gains reported when using spiral-wire reinforced models
Engineering Superiority in Fluid Transfer
Modern fuel oil delivery hoses incorporate four-layer construction:
- Inner tube: Oil-resistant synthetic compound (SAE J30 R9 certified)
- Reinforcement: Double steel braid (minimum 2,500 PSI burst pressure)
- Anti-static wiring: ≤10⁶ Ω/m resistance
- External cover: Abrasion-resistant polymer with UV stabilization
Manufacturer Comparison Analysis
Brand | Pressure Rating | Temp Range | Material | Certifications |
---|---|---|---|---|
AlphaFluid Pro | 300 PSI | -40°F to +257°F | NBR/Steel | API 16C, ISO 6805 |
BetaMarine XT | 450 PSI | -58°F to +302°F | FKM/Aramid | DNV, ABS |
GammaFuel Ultra | 600 PSI | -76°F to +392°F | PTFE/SS Braid | API 7-1, MIL-H-24425 |
Tailored Configuration Options
Custom fuel and oil hose solutions address specific operational parameters:
- Diameter variations: 1/4" to 6" ID with ±0.5% tolerance
- End fittings: NPT, JIC, or BSPP connections with optional RFID tags
- Specialized coatings for saltwater immersion (ASTM B117 compliant)
Operational Success Stories
Offshore Platform Case: Replacing standard hoses with PTFE-lined fuel oil delivery hoses reduced maintenance downtime by 40% annually. Power Plant Retrofit: Custom 4" ID hoses with thermal monitoring sensors increased fuel transfer rates by 22% while maintaining 100% leak-free performance over 18 months.
Advancing Oil Fuel Hose Technology
Emerging smart hose systems integrate real-time pressure monitoring and automated shutoff valves, revolutionizing fuel oil hose management. These innovations complement traditional mechanical robustness with digital precision, ensuring compliance with evolving API 675 standards for hydrocarbon transfer systems.
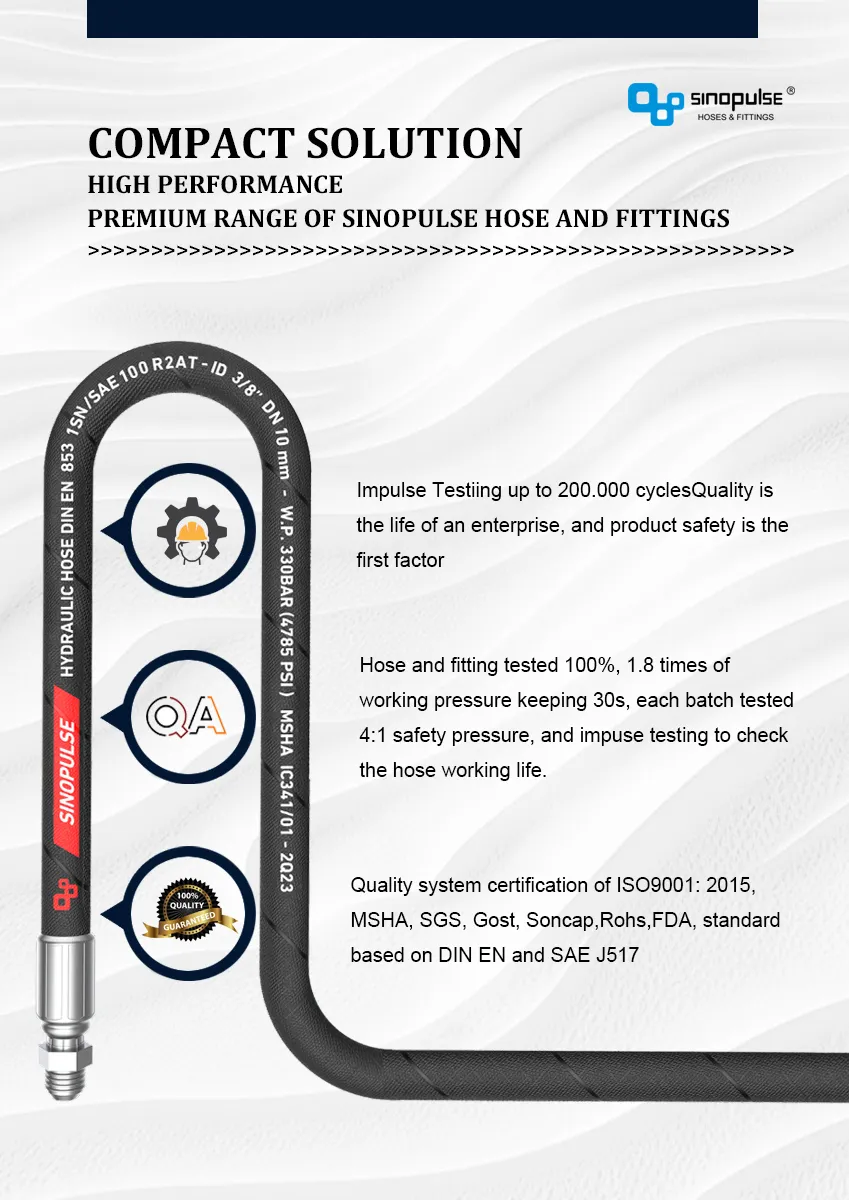
(oil fuel hose)
FAQS on oil fuel hose
Q: What are the primary applications of an oil fuel hose?
A: Oil fuel hoses are designed to transfer fuel oil in industrial, marine, or automotive systems. They handle high-pressure delivery and resist degradation from hydrocarbons. Common uses include fueling equipment and engine supply lines.
Q: How does a fuel and oil hose differ from standard hoses?
A: Fuel and oil hoses are reinforced with materials like NBR or CR for chemical resistance. They withstand fuel/oil exposure, unlike standard hoses that may degrade. These hoses also meet stricter safety standards for flammability.
Q: What factors determine fuel oil delivery hose selection?
A: Key factors include operating pressure, temperature range, and oil viscosity. Compatibility with additives and flexibility for routing are also critical. Always verify compliance with industry certifications like EN 1762.
Q: How often should fuel oil hoses be inspected?
A: Inspect fuel oil hoses every 6 months for cracks, bulges, or leaks. Replace immediately if abrasions or softening are detected. Follow manufacturer guidelines for specific service intervals.
Q: Can fuel oil hoses handle extreme temperatures?
A: High-quality fuel oil hoses operate in -40°F to 300°F (-40°C to 150°C) ranges. Specialty variants with silicone or PTFE linings extend temperature resistance. Always confirm ratings for your application environment.
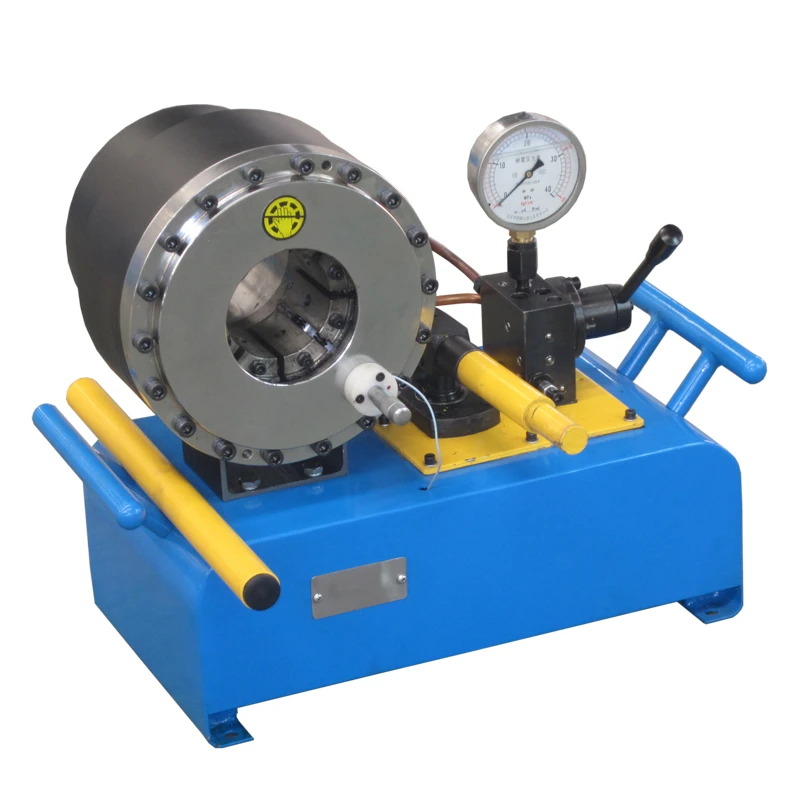
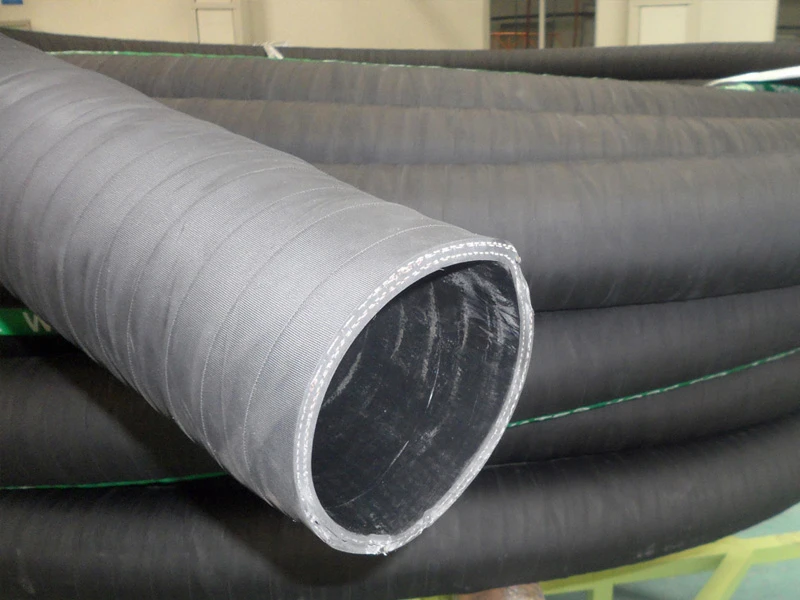
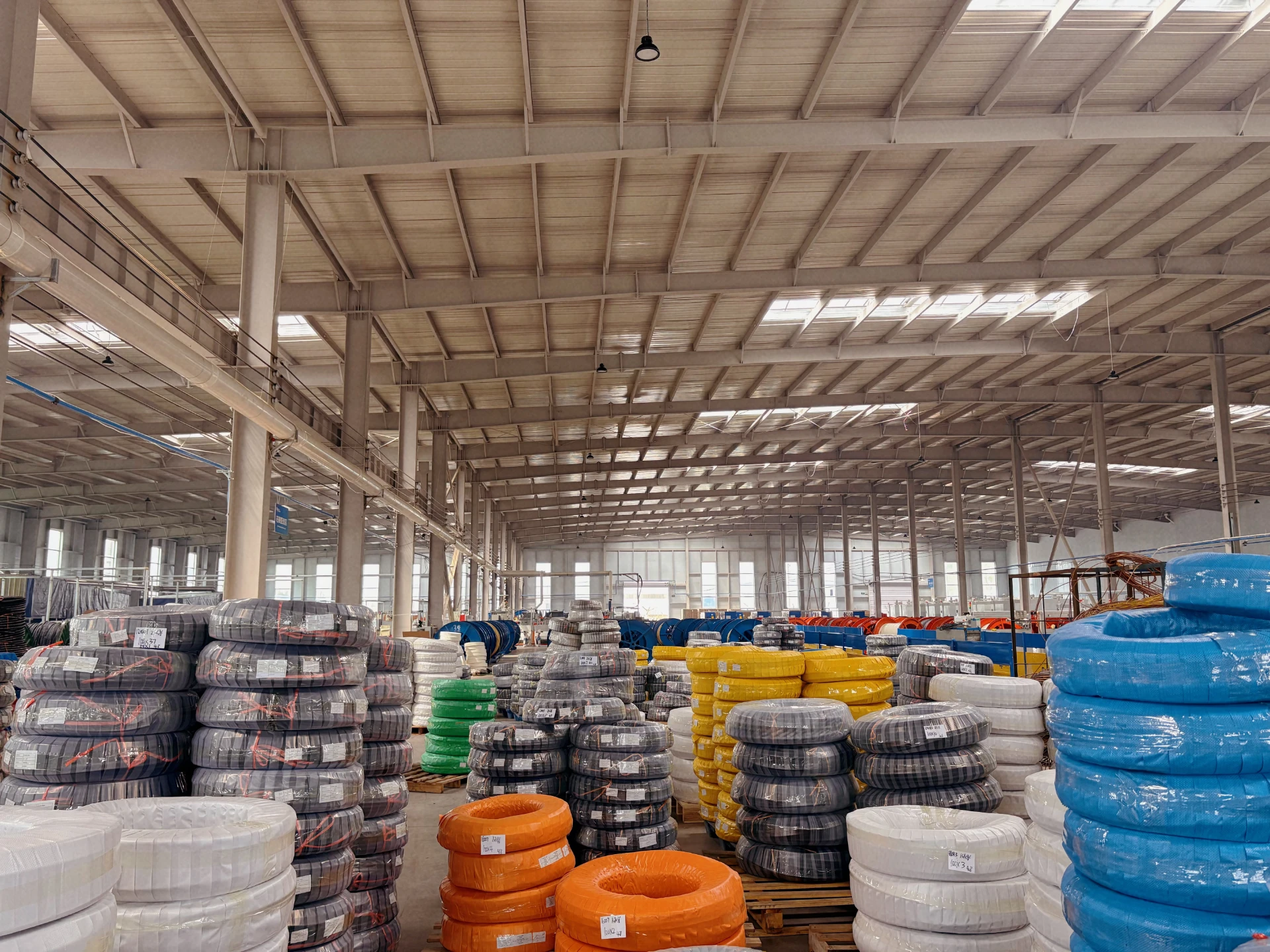
Product Application